The evolution of Digital Textile Printing alongside sustainable ink technology
.jpg?width=750)
Debbie McKeegan discusses how digital technologies are energy efficient and how production results in very little water usage. Digital textile printing offers a sustainable alternative to traditional rotary print routes.
The Textile printing industry crosses many disciplines, it’s a sector steeped in knowledge passed down over the generations by textile professionals. Over the last 20 years practitioners have converged to reform the technology now utilized in the sector. We often forget that behind each and every garment and each metre of print, there are hundreds (if not thousands) of product touchpoints and technicians who’s applied expertise generates each and every product that makes the journey from design through production and finally reaches retail.
The supply chain is complex and global, and yet for Textiles the process of printed manufacture is identical regardless of location. The Industry is struggling to reduce its carbon footprint and must gradually make the transition to clean, efficient production. Digital technologies that encompass all aspects of manufacture are in the early stages of adoption with just 6% of textiles currently being printed using digital technologies.
However, the digital textile print market is set to reach $266.38 billion dollars by 2023, that equates to 2.17 billion metres of printed textiles (source: Smithers Pira). The digitisation of the print route is well underway. Albeit at a slower pace than many would wish for if we are to make a significant impact towards reversing climate change and reducing the Industries current carbon footprint - which remains a sizable 10% of all global carbon emissions.
In our recent Fespa podcast Debbie McKeegan our Textile Ambassador caught up with Dr. Simon Daplyn the Global head of Marketing at Sensient Ink Technologies. Simon is a self-professed sustainability evangelist, and his doctorate in 2004 was a study of Digital Textile Printing specializing in ink formulation and chemistry. Simon has a deep technical knowledge of the textile sector, and an equal passion for the digital textile industries positive sustainability attributes. Here’s a summary of the key takeaways from our conversation.
Listen to the full Podcast <<Here>>
In the last 15 years the potential digital inkjet printing speed has skipped from 10m per hour to an astounding 90 linear meters per minute. There have been many technical advances required to reach this super-fast speed. Success can be attributed to industry wide collaboration within software, machinery engineers, print head technologies, chemistry and ink formulation professionals.
Digital Textile printing technologies now equal or even overtake the speed of conventional rotary printing when output is measured against speed of process. With an important and significant difference – digital technologies are energy efficient, production results in very little water usage and as such, digital textile printing offers a sustainable alternative to traditional rotary print routes.
The fashion Industry as an example is set to continue its seismic growth and its estimated that by 2030 printed production for the fashion industry alone, will consume 158 billion cubic litres of water per year. Much of the worlds industrial print is sourced from locations that are already short on water resources, and its predominantly in these locations that 20% of the world’s wastewater originates. Of this figure 8% is defined as from printed textiles. Green-house gas emissions produced during textile processing are currently 1.2 billion tons annually. Sources: Ellen MacArthur Foundation, United Nations, Greenpeace.
The technologies exist for the industry to switch to clean energy sources and alternate methods of production. As consumer awareness becomes a significant factor in the purchasing process, adoption of digital technologies is set to accelerate. Sustainable sourcing is now at the forefront of the supply chain as consumer behavior shifts in favour of environmentally sourced products. Labelling is increasingly required to deliver the provenance of the products offered for sale. The first step may very well be to quantify the products carbon footprint as we have witnessed in the food and packaging industry. Items must offer transparency to gain consumer confidence. The Covid-19 crisis has given everybody the opportunity to reconsider the throw away culture, climate change, over consumption, and raise awareness of the real impact of the textile industries carbon footprint.
The crucial benefits of digital textile printing are in resource efficiency and production agility. Compared to rotary production, digital uses a fraction of the energy consumed in traditional printing. Other benefits include the reduced chemical consumption and huge savings on the water needed for processing and printing. Digital textile printing presents a compelling argument for sustainable manufacturing, where alongside numerous benefits, carbon emissions can be reduced by as much as 80% using digital technology. Waste is not often discussed when considering the value of print, and yet the ability to print on demand delivers valuable reductions in unused meterage, unsold products and precious resources.
Covid-19 has placed a strain on the world’s textile supply chains. Digital technologies offer the ability to restructure the traditional supply route and a pressing opportunity to reap the benefits of print-on-demand by moving to a flexible, agile supply base that’s located closer to the consumer. But there are issues, and this switch demands investment and the replenishment of manufacturing resources. Sewing skills are in short supply and the world is also heavily reliant on China for polyester, currently China supply almost 80% of the polyester textile printed globally.
The digital textile industry has evolved over many years, and innovations in ink technologies have had a significant part to play in the speed with which jet technologies now deliver printed fabrics at 90 metres per minute. Whilst the inks used in rotary and digital are of the same source, their preparation for digital manufacturing requires the appliance of science. The first digital inks were reactive and dye sublimation which launched the technology; however, pigment ink is the most popular ink for traditional production and still holds roughly 50% of the marketplace. Digital pigment technology is set for huge growth as over the years advancements in chemical formulation have developed to offer high speed production. One of the strongest benefits of pigment production using digital tech, is that it’s almost a waterless process. Fabric is printed and heat-set, and ready for end use.
Caption: Innovations in ink technologies continue across all digital ink sets which improve both colour gamut, print quality at speed, and application diversity for specialist fabrics and market sectors.
Another sustainability benefit for digital production is the use of eco-friendly inks. Compliance to the United Nations SDG’s initiatives and the removal of hazardous chemicals via the ZDHC (roadmap to zero) compliance, have dramatically reduced or entirely removed toxic chemicals from the textile supply chain.
Caption: Direct to fabric printing is increasingly popular for dye sublimation inks, here both ink suppliers and paper manufacturers have collaborated to reduce the weight of papers, increase paper absorption and reduce total ink usage.
As the technology for digital printing advances, its inherent sustainable credentials cannot be ignored by the traditional textile industry. Affordability alongside performance will drive sustainable change and reduce the industries carbon footprint, whilst delivering product diversity at scale, alongside sustainable manufacturing.
Caption: The textile industry is set for growth, as printed meterage increases the technologies and inks that we choose have never been more important.
Interested in joining our community?
Enquire today about joining your local FESPA Association or FESPA Direct
Recent news
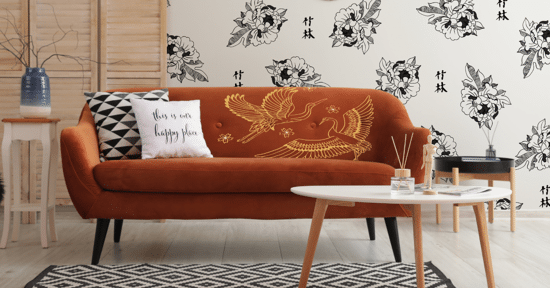
The power of digital design tools in screen printing
James Gatica shares how the combination of traditional screen-printing techniques with cutting-edge digital design tools is revolutionising the way designers conceptualise and produce custom decorative pieces.
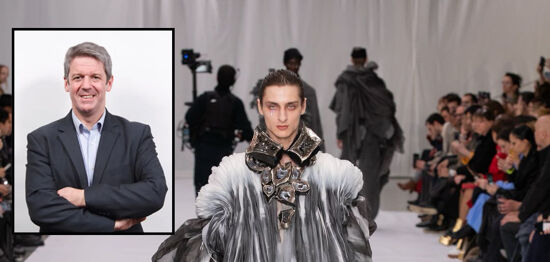
Key trends and market shifts on Personalisation and Sportswear with Epson
Debbie McKeegan speaks to Duncan Ferguson, VP of Commercial and Industrial Printing at Epson Europe about the market shifts and current trends around personalisation. Duncan shares the key trend of merging both fashion and sportswear.