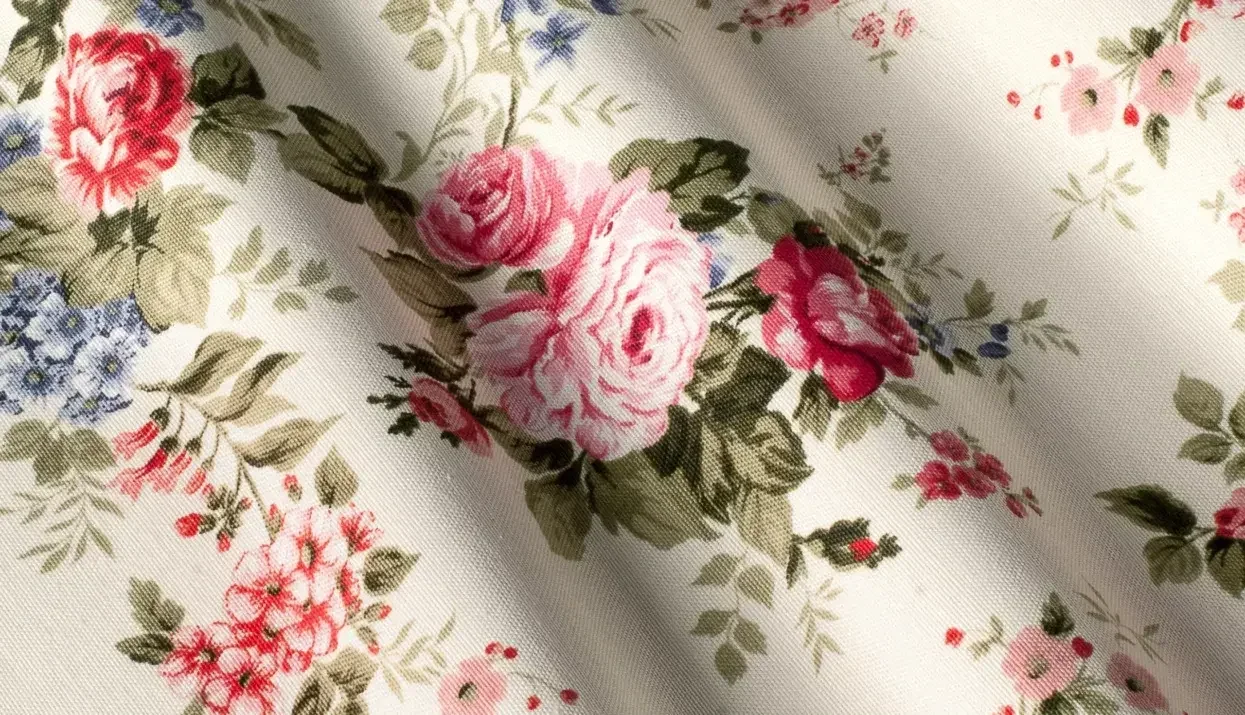
As we advance into a new decade, the growth of the Textile sector shows no sign of abating. In fact, as the world’s population continues to swell the growth of printed textile production and the availability of printed products is set for accelerated growth in-line with increasing demand.
Over the last twenty-five years the textile printing marketplace has changed considerably, and in order to meet the markets evolving expectations, so have the technologies that we utilize to manufacture the many billions of meters of printed textiles that we produce each year. The Textile industry is a diverse industrial sector with many, many layers, and it’s as those commercial layers have evolved – that established marketplaces have diversified and now offer a myriad of new opportunities that the traditional textile industry previously didn’t yield.
Much has been said of the growth of Fast Fashion, which for the last twenty years has dominated rotary production, with huge volume orders traversing the globe to meet the demands of a consumer that has grown to become more demanding, both in terms of design diversity and speed to market. However, we often ignore the volume of print that is generated to service the home furnishing marketplace which is equally diverse and offers a market primed for digital disruption. SPG Prints (formerly Stork) have a historic footprint in all textile printing markets, as the leading supplier of high-volume rotary production equipment and inks serving the industry since the company was founded in 1947.
The company first entered the textile market in 1953 with a flat-bed textile printing machine. In 1963 SPG Prints launched the ground-breaking RD-1, together with the world’s first seamless circular screen. For the first time, high speed rotary textile printing was possible, and its these innovations that were the foundations, thus enabling the mass production of printed textiles across the globe.
In 1991 SPG Prints launched the first digital textile printing machine – that was just the beginning of three decades of digital innovation that would lead us to where we are today as the digital textile sector expands to challenge rotary production.
In our recent podcast we interviewed SPG Prints – Jos Notermans, Business Manager of Digital Inks to discuss their journey to Digital and the future of hybrid textile production using both digital and conventional technologies. Here’s a short summary of the key takeaways from our conversation. << Listen to the full podcast >>
Turn back time – In the 1980’s Stork as it was then known conducted a study into new technologies that might perhaps replace rotary screen printing and decided that they wanted to own that technology as well. The outcome of that study in 1987 predicted that digital textile printing would replace rotary by the year 2000.
In 1989, Jos Notermans joined the company direct from university and has been with SPG Prints since the birth of their very first advances into the field of digital textile production and the parallel development of technologies for the graphics industry. As it turned out, by the year 2000 only 1% of printed production was digital, so the study was 99% off target, but nevertheless the foundations were in place.
In 2002 SPG Prints opened their own print production plant in Thailand to prove and advance their technology, Jos ran this facility until 2007 when he returned to Holland to run the business as it is today alongside the continued development of SPG inks and machinery.
In 2021 it is estimated that approximately 8% of textile production is printed using digital inkjet technologies worldwide.
Wide Format Graphics was the first application to embrace digital textile printing, and as such the technologies were built for high resolution graphic output. In order to convert rotary production to digital, print head technology needed to advance to meet the specific demands and the quality of established traditional textile production, increased speed and multiple ink sets. It was apparent that SPG needed to develop a new technology that was built for textile production at high volume. Graphic print heads are designed to print at close proximity to the substrate, however for textiles, head height is a contributing factor to production quality, speed of production and print mark continuity. It was this research that defined the founding principles and the roadmap for the development of the SPG Prints – Archer technology.
It was also clear that as technology was advancing at great speed the customer required a secure technology, and a future safe investment that would not be rendered obsolete in just a few years. It was therefore decided that the head technology would be independent of the machine’s electronics, and as such could be replaced as required and as technologies advanced.
Caption: Over the last three decades printing speeds have accelerated, with the very first digital textile machine printing at just 1m per hour – today in 2021, the SPG Archer platform offers print speeds ranging from 40-80 metres per minute. Image Credit: SPG Prints.
It’s worth noting that when digital textile printing was first introduced (1991) designs could not yet be seen on a colour computer monitor. Prior to windows 95 – when programming pixels, the first visual was when the file was actually digitally printed onto fabric. “We have come a long way over that last 25 years or so and have met our client’s expectations – digital printing machines now run faster than rotary, when you factor in production downtime for screen changes and washing by comparison. The print conversation is no longer about speed and has turned to focus on sustainability”.
Ink technology has also been a considerable factor in the innovation of the print workflow, the inks used in traditional rotary printing are not suitable for digital production, they contain heavy meals and other contaminants that are not compatible with inkjet head technologies. Manufacturing digital ink is therefore much more expensive than rotary, impurities must be removed, and the pigments milled and refined for digital production. At the turn of the century one kilo of ink was valued at approximately 125 euros, still a considerable drop from the 700 euros per kilo in 1991. Nowadays, if you look at large volume customers the average price is around 15 euros per kilo, sometimes even less. The ink cost per square meter is still a dominant factor, when compared with rotary production – but you have to look at the bigger picture, the total cost of ownership and the commercial gains and benefits when utilizing digital machinery. “The breakeven point between rotary and digital (as a rule of thumb) is around 1000m, less than 1000m digital is always cheaper on cost. If you print more than 5,000m rotary will be more cost effective, but there are now so many more factors that come into play as part of the commercial argument”.
Caption: SPG Prints see growth in both rotary and digital machine sales as the textile marketplace expands using both technologies, often simultaneously. The market must evaluate the best solution on merit, which is always dependent on the client’s commercial reality. Image Credit: SPG Prints.
As the market matures Jos expects digital to reach 20-30% of the total available market with rotary providing the remaining volume – purely because the cost of digital is prohibitive in in the high-volume industrial sector where conventional print will remain. Innovations continue for rotary screen printing inline with the sustainable development goals just as they do for digital inkjet technology. SPG continues its RND for conventional printing, last year launching a new screen technology that reduces the required percentage of ink paste per square meter – all of which reduces the environmental footprint of the textile printing industry.
Hybrid production is already a key workflow for the textile industry, most of SPG’s customers offer both digital and conventional production which has been accelerated since 2010 by the advancement, stability and the speed now achieved by digital textile printing technologies like the Archer. There are a lot of things happening in the global sphere that will determine how the future will look, so in order to judge what is the right solution you should look not only at the cost of the ink, or the cost of the machine, or the price per square meter – buying behaviour will make a huge impact on how printed textiles are sourced and produced in the near future.
Going full circle back to where we started, it would be interesting to look at technology again – said Jos, what if we replaced inkjet? “We all thought that single pass would be the next big wave, but it didn’t happen, since 2015 there are perhaps fifty single pass machines – single pass wasn’t the breakthrough we predicted. I think the big breakthrough is yet to come and that’s probably to do with more reliable, cheaper print heads. If you look at the cost of the heads utilized in a single pass machine as a contributing factor, the total cost of multiple heads can be as high as 800,000 euros. If we can reduce the cost of the heads and electronics, we can half the cost of the machines – if we can do that, and I expect that we can in the next five years, we will have a break though technology and that will unlock single pass production”.
Caption: The voice of the customer is the most important voice – we have to stay close – we must understand their implicit requirements to ensure that the next generation of digital or conventional technologies that are in development meet the industries finite requirements. Image credit: SPG Prints.