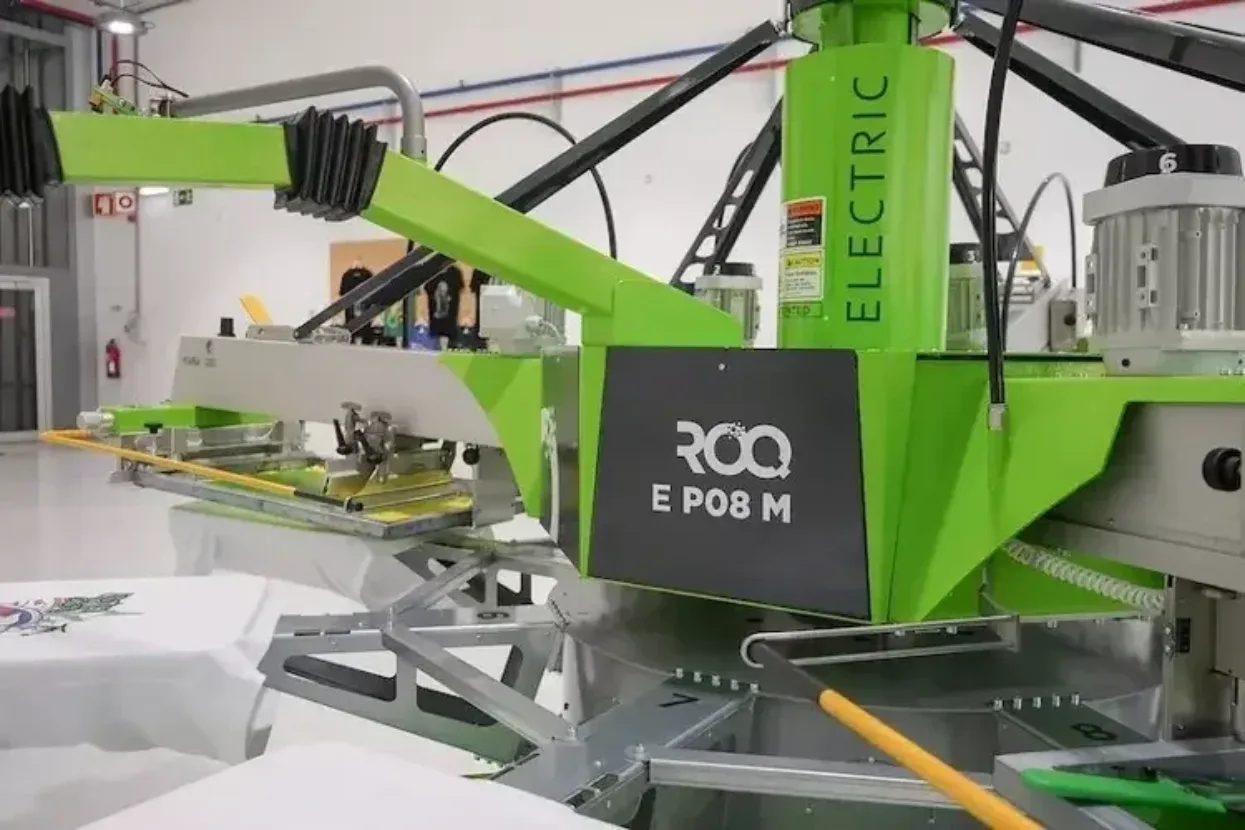
Screen printing may be a relatively manual process but there are a number of automated options available. Nessan Cleary emphasizes the importance of automating processes around screen prinitng machines in order to achieve excellent print results.
Regardless of what type of printing, every print business needs to be able to automate at least some aspects of production in order to both cut costs and take on more work to raise revenues. The current economic situation means that standing still is simply not an option, no matter what kind of business you are in. However, some print processes, particularly around digital printing, are easier to automate than others. Screen printing, by its nature, is more of a challenge to automate, but who doesn’t like a challenge?
When it comes to automated screen printing machines, there are two main designs: rotary and flatbed. With the rotary devices, the screen is mounted to a cylinder that rotates as the substrate passes. This is suitable for fast high volume production. It’s not uncommon, for example, to find a rotary screen printing unit on a flexo label press.
However, at a Fespa show you’re more likely to encounter the more common flatbed which will work with a wide range of substrates, including textiles for garment decoration. And an automated screen printer, whether carousel or oval, can achieve much higher productivity when printing direct to garments than most of the current inkjet DtG printers.
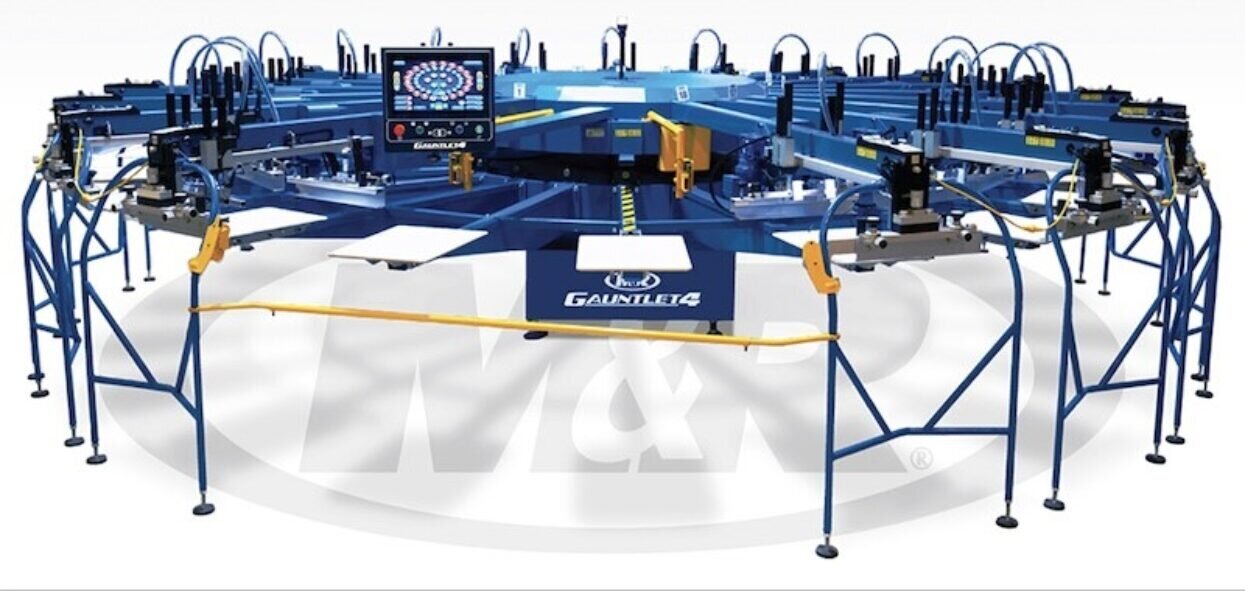
Most modern automatic screen printing machines are fitted with servo motors throughout, right down to the individual stations, which can give a very precise level of control, with those settings saved to memory for use in different production modes. This is a distinct improvement on the older chain-driven mechanical approach, where the chain could stretch and wear over time, leading to problems such as registration issues between stations.
Most automatic machines will also have some features driven by compressed air, particularly pneumatic frame locks. Such systems also allow for equal squeegee pressure between stations to ensure consistent ink laydown and colour density.
There’s been a general move towards water-based and discharge inks in recent years, which carry the risk of overheating after flashing. Consequently most modern screen printing presses will use lightweight aluminium pallets topped with rubber pads to prevent this.
Last summer M&R launched two new automatic screen printing presses, the Gauntlet 4 and the Copperhead Speedmaster. The Gauntlet 4 has a carousel design that’s been designed for high productivity and features an advanced pallet levelling system. It can be run clockwise or anti-clockwise and can be configured with up to 16 stations and 14 colours. It will print a maximum image area of 51x51cm. It uses a laser system to help users position garments precisely. The pallets have a built-in temperature sensor and can be pre-heated. The printheads can be automatically operated in a programmed sequence with multiple flashing. It includes a self-diagnostic system and will alert operators to any necessary maintenance.
M&R’s Copperhead division put together the new Speedmaster, which can produce up to 1200 pieces per hour. There’s a choice of 12 to 20 stations with a standard image area of 51x71cm. It’s been designed for quick set-ups with a touchscreen control panel, electric printheads, pneumatic frame locks and the ability to set squeegee and flood bar angle adjustments without needing specific tools.
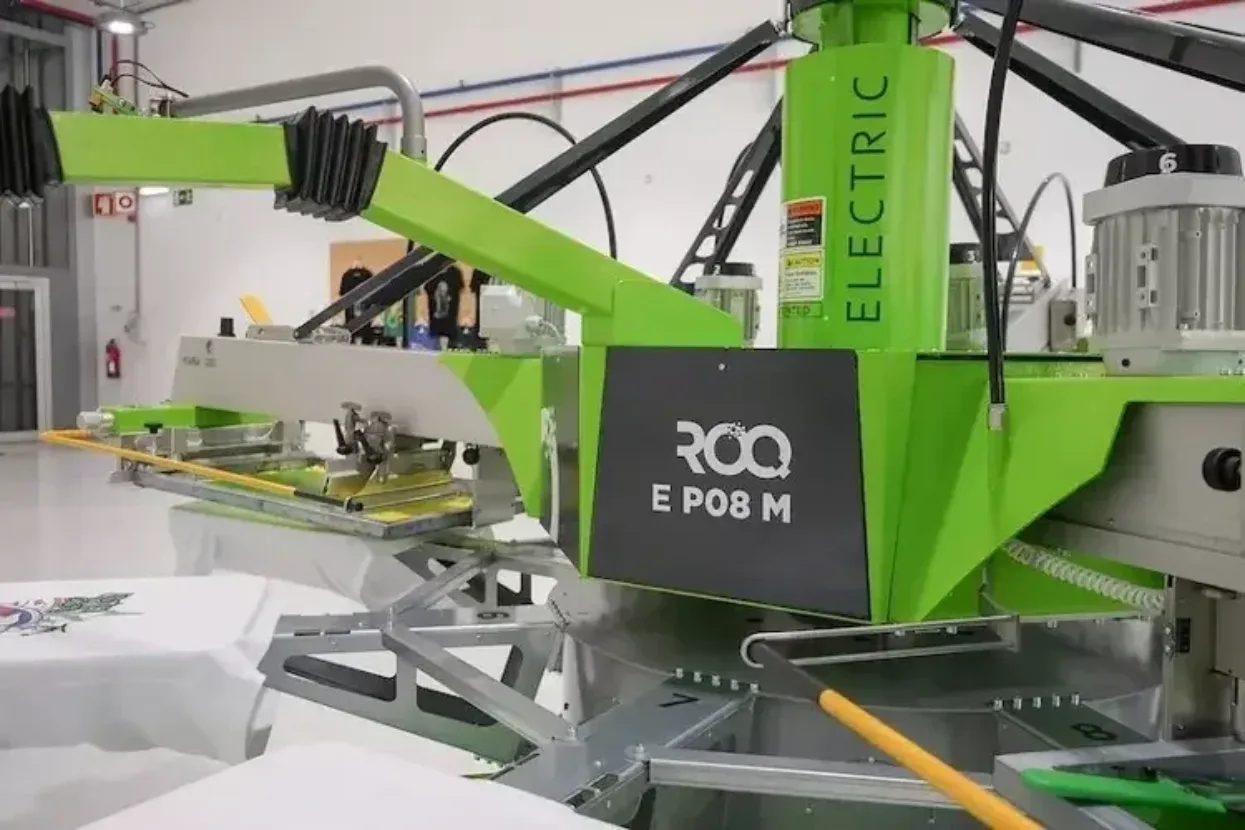
Last year Roq introduced a new electric screen printing machine, the Roq E, which is designed to do away with the need for noisy external air compressors. It uses a built-in air supply, which is said to be quieter and more pleasant to use, and installation should be easier since you only need the electric power. It’s a fully automatic machine and can produce up to 900 pieces per hour. There’s a choice of eight or ten stations with up to eight colours.
Adelco makes the Cyclone, an automatic carousel machine that’s available in three sizes of small, medium and large. These allow a choice of six to 14 colours, with eight to 16 print stations and with maximum print areas ranging from 45x50cm up to 60x80cm. It uses servo motors for the main drive and the printheads to give a higher degree of control while maintaining speeds of around 1000 pieces per hour. It has a touchscreen that allows for relatively simple set-up and also includes self-diagnosis for narrowing down any problems. There’s an option to add LED lights to the print heads to illuminate the screens during set-up and use.
MHM makes the iQ Oval, which has a modular design so that users can reconfigure and expand it up to 60 stations with up to 48 colours as their needs change. Each pallet arm has an independent drive system, which should prevent any registration issues between stations. The index drive motors should stop upon sensing any resistance, reducing the risk of operators getting hurt. The main control unit can be run from a tablet and there’s a control keyboard at every station. It’s available in four different sizes, with the maximum print areas ranging from 45x55cm to 80 x 110cm.
Flash curing is an integral part of screen printing, and most vendors also offer automatic flash curing modules, usually designed to fit specific machines. MHM, for example, sells the QC4170MW flash cure unit for the IQ Oval screen printer. This uses a microprocessor controller to automatically balance the level of curing needed without overheating to reduce the need for cooling stations. All the curing units can be controlled from the iQ Oval’s central touch screen display.
There’s little point speeding up the productivity of the printing stage if you don’t also consider automating the following steps in production. When it comes to drying, that mainly means using a dryer that includes a conveyor system. There’s a choice between gas and electric, with gas dryers generally offering better control over temperature and higher drying capacity.
It’s also worth looking at how to automate the fulfilment stage. M&R’s Amscomatic division, for example, makes several automatic post-press machines, such as garment folders. The K950, for example, can automatically fold a wide range of different garments and can store up to 99 fold patterns. It can be used in conjunction with the LS-350 long sleeve folder, which takes long sleeve garments, folds the sleeves and then passes the garment to the K950. These can be used with other devices, such as the AB9000 automatic bagging and sealing machine. Putting together a folding and bagging line can take out any bottlenecks in the production, as well as reducing the amount of manual work needed.
In conclusion, modern automatic screen printing machines can achieve excellent print results while maintaining high productivity. But to get the most out of them you also have to automate all the processes around them, from making the screens through to folding and bagging the finished garments.
Discover the latest innovations in automation and screen printing at FESPA Global Print Expo 2024, Europe’s leading print and signage exhibition. Taking place from 19th – 22nd March 2024 at RAI Amsterdam, Netherlands. Register here to visit and use promo code FESJ404 for a 30 euros discount.