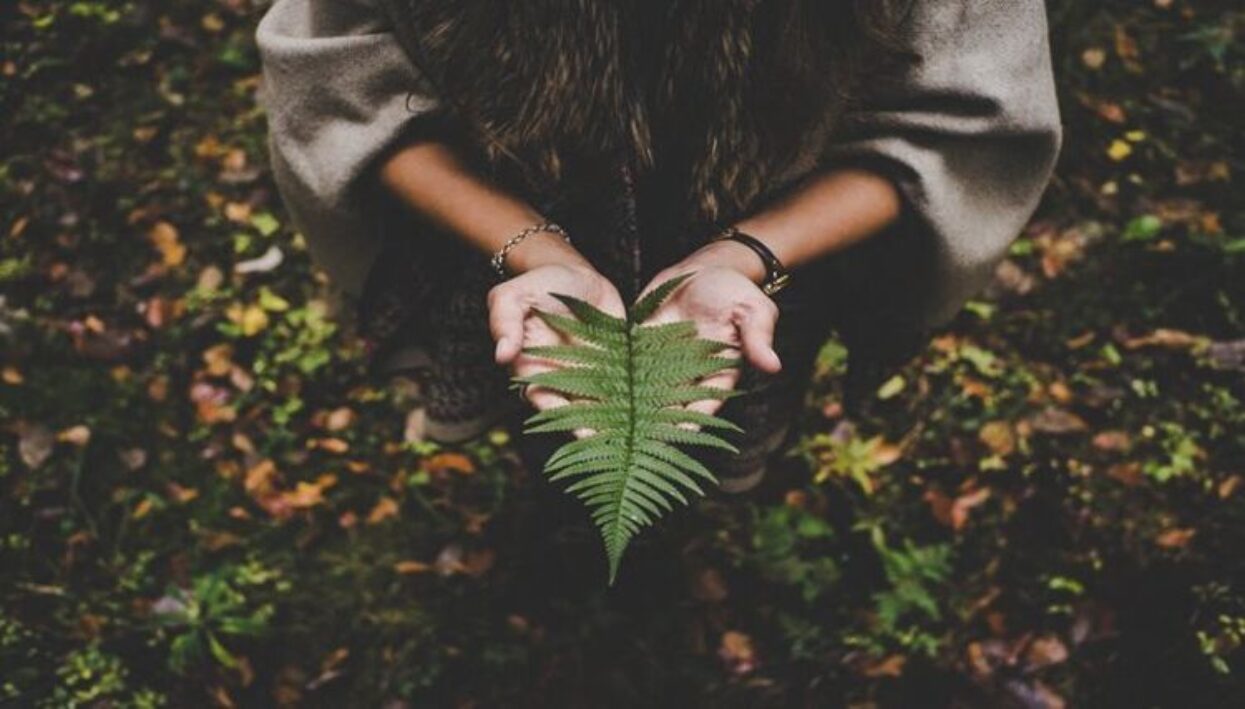
Laurel Brunner discusses this history of computer to plate technology, the important role it plays today in the print industry and how it influences print media production workflows.
It is astonishing how long it took for computer to plate technology (CtP) to become prevalent. CtP in prepress has made a substantial contribution to the improvement of print’s environmental impact. By going direct to plate and bypassing the film imaging and contacting stages eliminates processes in printing plate production. CtP has existed since the 1980s, however its key goals have proved to be rather elusive. This all changed in 1995.
The CtP breakthrough occurred at Drupa 1995 when developers finally solved the problem. They searched for the elusive combination of coating and processing chemistries. Their goal was to have short imaging times and long run length on press with cost-effective imaging layers and processing chemistries.
In 1995 Kodak and Creo (which Kodak later acquired) introduced thermal imaging CtP. This entirely upstaged introductions from competitors which presented various CtP devices based on green (YAG) lasers. At Drupa 1995 there were more than 50 CtP systems from companies who had fallen by the wayside or been acquired. These included Autologic, Cymbolic Sciences, Purup, Barco and Creo.
Agfa’s LithoStar was the first real CtP plate which was introduced in 1993. Other options were made available by Fujifilm with Brillia and Kodak’s electra plates. Today there are very few imaging systems sold or implemented in developed markets. Kodak continues to sell a lot of film in some countries but CtP and associated plates are replacing ageing film systems.
CtP has become the norm for most workflows and this technology continues to reduce the environmental impact of print as companies improve their plate offerings. Processless plate technologies continue to get better and developers have created interesting innovations for how they are sold. For example, Agfa offers customers the option to buy only the imaging layers, so they efficiently rent the plate’s aluminium, which Agfa then collects for recycling as part of the deal.
In the more recent years, we have noticed customers moving towards processless plates which don’t have the durability of competing options. However, this is not an issue as print run lengths fall. Kodak reports increasing sales for its Sonora processless plates across all geographies.
In addition, CtP has influenced other areas of print media production workflows which helps to improve print’s sustainability. CtP drives improved processing, energy requirements, data accuracy and overall production speed. It has helped create an environment where numerous companies can thrive, developing software that helps to ensure that prepress errors are managed early in the workflow and electronically. In addition, CtP has increased the importance of accurate digital data processing, errors on plate and press are expensive to fix. Fortuitously, advances in prepress means that such disasters are quite rare. Fewer remakes means less waste and another boost to print’s environmental impact.
Source: This article was produced by the Verdigris project, an industry initiative intended to raise awareness of print’s positive environmental impact. This commentary helps printing companies keep up to date with environmental standards, and how environmentally friendly business management can help improve their bottom lines. Verdigris is supported by the following companies: Agfa Graphics, Spindrift.click, EFI, FESPA, HP, Kodak, Kornit Digital, Ricoh, Splash PR, Unity Publishing and Xeikon.