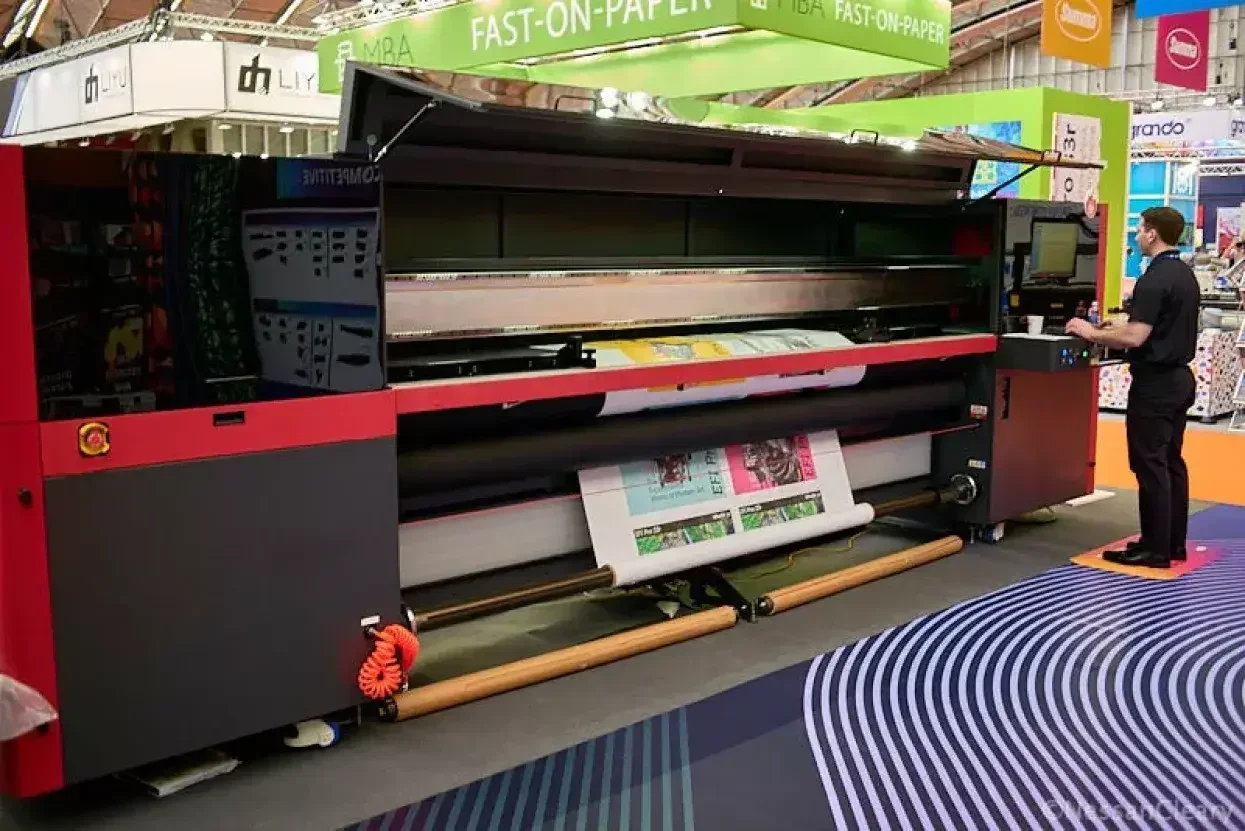
Nessan Cleary discusses the different ways you can improve your maintenance and how this can lower your machine downtime. He emphasizes the importance of having a service agreement.
Every new bit of kit comes with an accompanying announcement as to how easy it is to use and how intuitive its controls are and how many processes have been automated. But the reality is that wide format printing is an industrial process and each item of equipment is itself a complex mix of components and sub-assemblies that need to be operated and maintained in a particular way.
More to the point, all of this equipment is expensive and is only earning its keep when it’s running. So it makes good business sense to pay particular attention to the maintenance, to prevent any unplanned downtime and keep those machines working.
Besides this, the best way to prevent problems with an inkjet printer is to keep it running. The constant flow of ink through the printheads helps to clear any blockages and prevents the risk of the ink drying on the nozzle plate and potentially clogging the nozzles. That said, you will have to pay attention to those channels, such as a white ink or a clear varnish, that might not be used as frequently as others. Many printers will include recirculation on their white ink printheads, which will considerably reduce the risk of blockages but you will still need to carry out routine maintenance.
Otherwise, the starting point for having a proper maintenance regime is staff training, which is sometimes seen as a burden in terms of time and money. But your staff are working directly with the machinery so investing in their career development is the best way of protecting your capital investments. Schedule time within each shift to make time for maintenance, and ensure that staff keep a regular log of what they are doing so that you can check back if there are any problems.
The most important aspect of maintenance is cleanliness, from the printheads right down to the floor in your production space. Keeping the shop floor clean will prevent dust causing problems as well as limiting the potential for accidents and injuries. It may be worth investing in dust covers for any equipment that is not used regularly.
When it comes to printers, the biggest risk is blockages to the nozzles which could force you to replace expensive printheads. Piezo printheads should last for several years but the key is to keep them clean. Many of the more expensive, high volume printers can run automated cleaning routines but they should still be routinely inspected for best performance. It’s also a good idea to regularly print out test charts and ensure that all the nozzles are firing and that all the colours are still within tolerances as this will also alert you to any potential issues.
In most cases, you will have to manually clean the printheads, which means physically wiping excess ink away from the nozzle plates, whilst being careful not to physically touch the nozzle plate. The frequency will vary from one printer to the next but a good rule of thumb is to clean the heads at the start and end of every day or between shift changes. And of course you will have to use the right materials and keep a good stock of lint-free wipes and the appropriate cleaning fluids.
Besides the printheads, you should also inspect and clean the area around the print carriage to prevent any ink or dirt from building up. Don’t forget to check the guide rails and bearings as well as the media feeding for any build up of dirt that might interfere in the printer’s operation, and to keep moving parts properly lubricated.
Whilst the printer is still under warranty, you should use the manufacturer’s own ink so as not to void the warranty and any maintenance contracts or insurance that you have for that machine. There are numerous third party inks available, particularly for solvent, latex and textile printers. Naturally, the manufacturers will advise using their own inks, and this is certainly the safest course since the ink will have been designed to work with that printer. However, there may be an economic argument for using third party inks with an older printer though you should check carefully how compatible those inks are with your particular printer. Whichever ink you use, check its recommended storage conditions and don’t use anything beyond its shelf life.
In general, inkjet printers will require the most attention but don’t forget the rest of your equipment. Everything will benefit from being kept clean, and from carefully following the manufacturer’s recommended maintenance. You should also check the associated tooling, to ensure for example that cutting blades are still sharp enough to produce clean cuts. You should pay particular attention to any cutting equipment where there is an obvious health and safety risk to staff.
As well as the hardware, you will also have to maintain your software. At the very least you should ensure that all software is fully up to date, from operating systems to printer drivers and that all security patches have been applied. Don’t forget to check that any new versions of software will be compatible with other software or equipment that you are running.
In today’s connected world it’s equally important to maintain all your software.
©Nessan Cleary
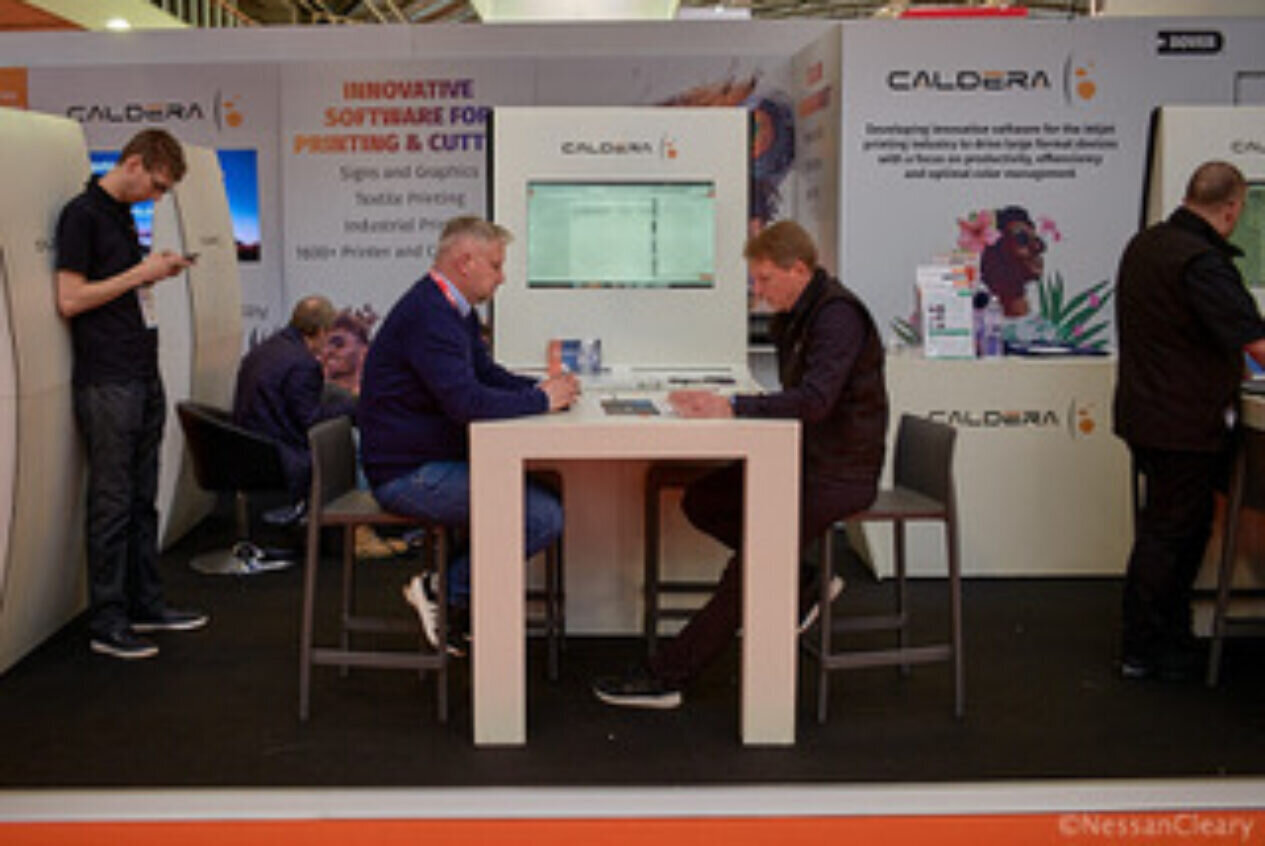
Besides the equipment, you should also keep the building well maintained. A leaky roof will lead to rain damage, while a weak floor may affect the print quality if the printer vibrates whilst the head carriage moves. Ideally the temperature and humidity around the printers should be reasonably stable as sudden variations might affect the output, particularly the colours.
Chemicals should be safely stored and the building electrics checked regularly. It’s a good idea to fit surge protectors to all of the equipment to prevent sudden power spikes from damaging their electrical circuits – but you will have to periodically make sure that the surge protectors themselves are still working.
Finally, you will need a service agreement for just about every piece of equipment you are operating. This agreement should contain all the details of what you are responsible for and what your servicing agent will do, plus the costs and timing. You can reduce the cost of this servicing, and cut down emergency call-outs, through good maintenance processes, which will more than cover the time and cost of making this effort.
To discover the latest content that covers a wide range of sectors including automation, software and cutting sign up for FESPA’s free monthly newsletter FESPA World available in English, Spanish and German.