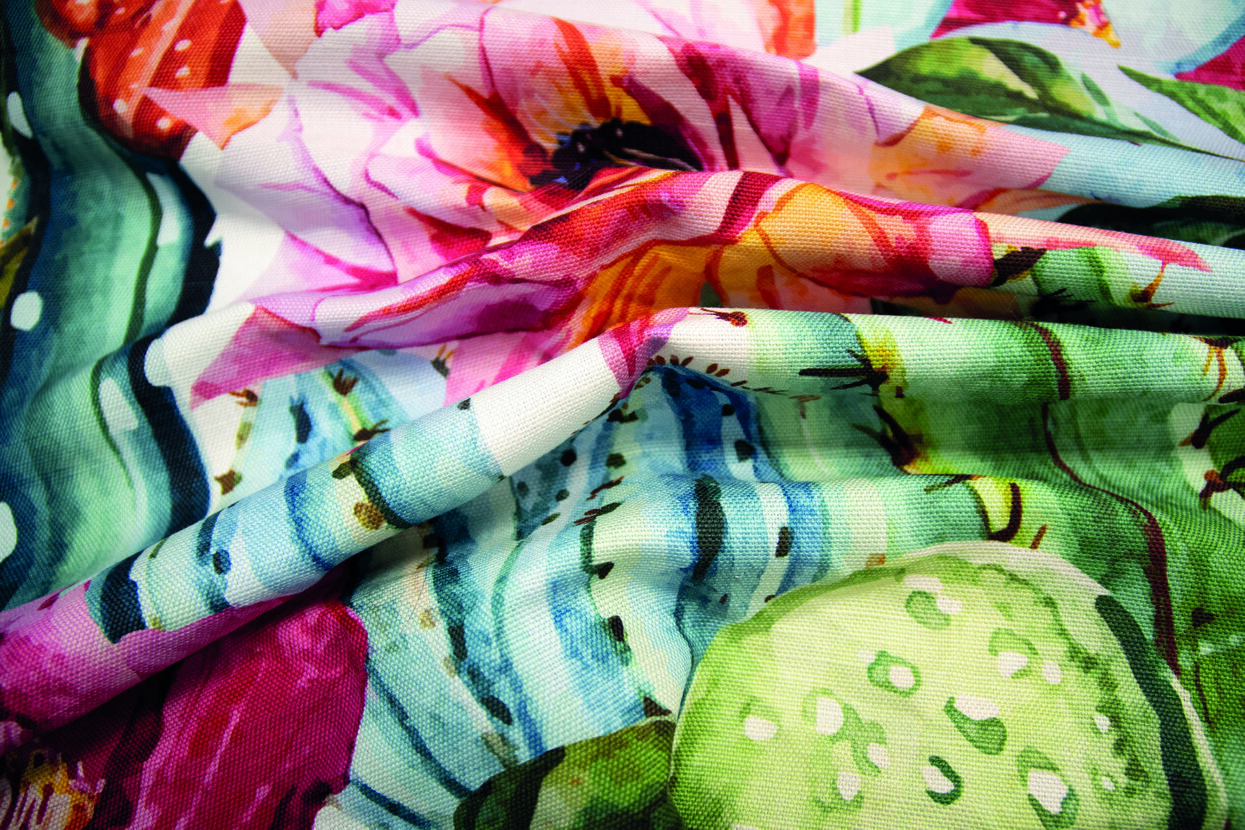
Over the last 140 years Zimmer Austria have pioneered many innovations and revolutionary technologies for screen and digital printing, coating, dyeing, steaming and technical textiles.
Zimmer technologies serve applications for areas such as home textiles, wallcoverings, fashion, upholstery, towels, blankets, technical textiles, nonwovens, paper and even glass fiber.
In our recent podcast we invited Tony Naschberger, the CEO of Zimmer and Andreas Rass, commercial director to discuss Zimmer’s history, technology and how their innovations continue to disrupt the textile and carpet industries. Here’s a summary of the key takeaways from our conversation:
Zimmer has two manufacturing sites one is in Kufstein which is focused on taking care of all issues related to digital printing and carpet manufacturing. Based in Klagenfurt, Austria the second factory, is taking care of screen printing and textile coating machinery. Zimmer started digital printing about 45 years ago, when they introduced a printing technology originally named Chromotronic, which was renamed later to become the technology we all recognize as Chromojet.
Since then, Zimmer have pioneered many specialist innovations for digital printing which is what differentiates them to their customers and from other companies. Number one – Zimmer invest in process technology. They not only build printing machines but also deliver a lot of process know-how, essential as the industry evolves from analogue to digital. Zimmer deliver complete lines including steaming, washing, drying, coating, and have a wide network of strategic partners, including chemical suppliers and fiber suppliers. “I think that makes us very unique and Zimmer are very well known for our service. Especially in digital machines – service is key for success” commented Tony Naschberger.
Zimmer began their digital journey in around 1976 – how do you think digital technologies have disrupted the textile and carpet industry?
Tony Naschberger:
“In 1976 we had the idea to do something digital but at that time digital printing was not existing at all. And so, we built wealth-based machines, the Chromojet or Chromotronic as it was known at that time. We were really suffering from a lack of available technology back then – I mean, we had to drive the machinery with HP main frame computer with 256 kilobyte of memory, the first hard drive being just 5MB megabyte – but that was just the beginning”.
Image credit: Zimmer Austria
Over the last 46 years Zimmers vision and early innovations were the building blocks of the Chromojet technology that would go on to disrupt the carpet industry which now almost totally serviced by Zimmer’s pioneering machinery.
Zimmer’s textile printing technology offers the industry an ecological solution. Tony commented further “Finally, we will also see digital disruption in the textile industry – almost everything is moving digitally. And we are part of it. We don’t have to discuss the advantages of digital printing today – the next shift – is not driven by technology. It is ecological. Because we are we are short in water, we are short in energy, we are short in anything and everything. And digital textile printing is one of the way’s out.”
Having seen such an incredible transformation in the carpet industry? How long did that take? And did the disruption accelerate quickly?
Tony Naschberger explained: “I think it took us almost 10 years to stabilize the technology and also to bring the advantage to our customer. But later uptake accelerated. And I think it typically took almost 20 years to really gain market share in the carpet industry. And I see more or less the same in in the textile industry. Maybe it’s a little bit faster, but it takes time”.
How big is the carpet industry by volume meterage? As an indication of scale, how many meters are now printed digitally every year?
Image credit: Zimmer Austria
So, our latest estimate is around 200 to 250 million square meters are digitally printed annually around the globe, it’s a really significant amount. And compared to maybe only 20 million square meters, which are printed using screens. 90% of carpet printing is now digital – it’s a significant difference between screen print and digital print. You see how far the technology is placed in the market and how it has replaced the screen-printing carpet sector.” commented Andreas Rass.
It will be interesting to have this conversation again, in five- or six-years’ time and compare those stats to digital textiles and see how that’s swinging.
Where is the biggest volume of carpet manufactured and do you see a swing towards reshoring in the carpet industry?
Andreas explained – ”It’s a big question. Certainly, the biggest volume is manufacturing still in the US. Globally, it’s the biggest producer of carpets, but it’s also the biggest consumer of carpets. You see a significant installed base and also production capacity in China, Turkey, Egypt, Belgium, which has a long history in carpets, but you also see some growing countries like Uzbekistan, for example, those are countries which are just ramping up. What we see is a trend that some of the Chinese production is moving to India and Turkey. So capacities are shifting a little bit. There are different reasons for that, but certainly one of the reasons is political, that some countries especially big carpet producing countries are introducing market regulations, which make it very, very difficult to import into the domestic market to protect the local carpet manufacturing. So we all have to deal with it, our customers have to deal with it, that’s the nature of the business.
Where we clearly see the high price, segments are staying close to the customers, where they are selling them, because quality, short turnaround, times stability, in supply and quality, this is key. So this is not something that you see going away from the higher price countries to lower price countries. And when it comes to promotion products, where we have especially our logo, matts customers, or the promotional towel printers, this will always stay very close to the market because the short runs the short turnaround times – this is key for this market sentiment”.
Which sectors of the marketplace and which product groups does Zimmer digital technology now serve within the Textile Industry?
“For the last 10 years, we have the Colaris digital textile printing system in our product portfolio, which we use for heavy textiles applications, but also for carpet printing, very successfully in the last years. All this technology comes together as mentioned with the necessary pre and post treatment. So from entry unit down to the steamer washer dryer, even color kitchens if necessary. We have a very broad range of fibers that we can print onto. We have reactive inks for cotton, and we have acid metal complex inks for nylons with disperse inks for polyester printing. Pigment printing is also part of our portfolio. But we also have another specialty, where not many others are stepping in, which ink for acrylic or modified polyesters.
Image credit: Zimmer Austria
Zimmer also service VAT inks which give you the best lightened wash fastness” commented Andreas Rass “We have two lines running now in the UK which is it’s quite a big step forward in the in the digital printing environment. In the textile segment, we are still very much focused on the heavier fabric. Because this is where we are coming from and this is where we feel comfortable to add value to our customers that we’re talking about; Terry towels, upholstery, furniture, fabrics, window fashion blankets, heavier bed linens, so a pretty broad portfolio.
Zimmer also supply machinery for technical textiles, and specialise in military camouflage printing.
Andreas commented further: “So not only the decoration of a fabric, but also to functionalize the fabric with infrared reflectance control and in all these applications, we are able to build machinery here in Austria and sample for our customers. That’s quite an interesting field we want to go into much further in the future. In a similar area are the narrow fabrics, so belts and ribbons, especially the belts, there are a lot of military applications that you see nowadays. With our broad portfolio of printheads and available applications, we have also stepped into the other OEM development partnerships. So serving two partners, technology for additive manufacturing, for example. But this is something what we do pretty much outside of our standard business setup – we are constantly evolving – Nobody can ever stand still.”
What does the future hold for on demand production and how do you think this sector is going to continue to evolve?
Andreas Rass: “A big thing for us and our customers – but also the for the consumer – is the sustainability of the process and of the final product. We are all aware in the carpet and textile industry that we’re in a resource consuming industry when it comes to energy and to water consumption. And there are things we need to work on as a whole manufacturing eco-system. Just talking about printing – maybe – moving more into the pigment printing field, which demands the acceptance of the market and of the consumers. You have a different fabric touch, you have different fasteners level, but pigment comes with a lot of ecological advantages.
Where we also see change – is within the lifecycle view – that having a sustainable final product does not mean only the wet process or the finishing process needs to be improved. We see for example, that that you need to start working already at the raw material level – at the fiber – to modify your fiber for example: Polyester with disperse printing is also very energy and water consuming process, if you modify your polyester and have a bionic polyester for example, you can use different dyestuff. Which is going to reduce the process time, energy consumption and water consumption by more than 50%.
So, those are things the market is going to move towards and we will be certainly part of it. And when it comes to recycling – if you look at carpet – the carpet has a different fiber at the pile, the packing is a different material, the back coating is a different material, it’s almost impossible to recycle this carpet. We will see new innovations in this sector as it moves towards more single material structures, which will significantly improve recycling. The only solution must be to build a more sustainable textile and carpet manufacturing environment”
Special thanks to Tony Naschberger and Andreas Rass of Zimmer, Austria. To listen to the full podcast please click here.