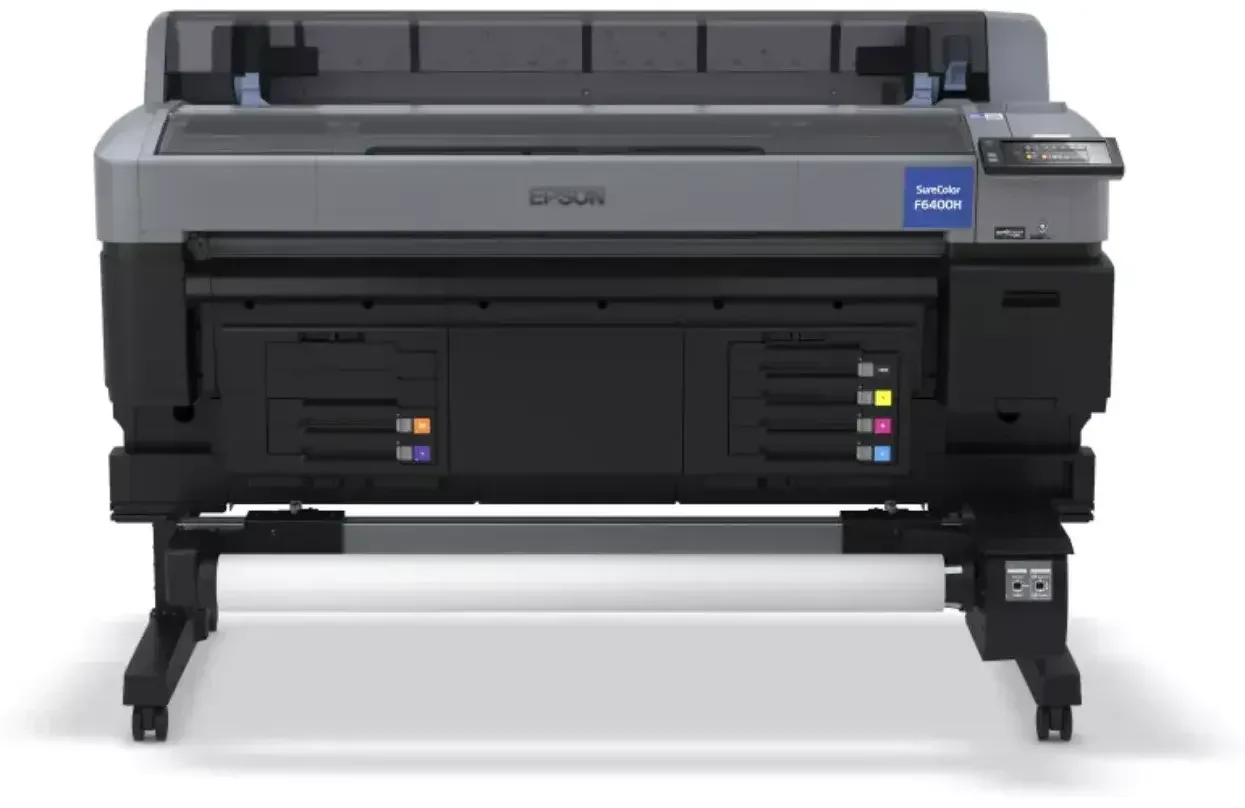
Paul Sherfield discusses how the latest implementations of Extended Gamut Prinitng demonstrate the several advances in ICC colour management, process control as well as instrumentation in recent years.
One of the ‘hot topics’ in the graphic arts areas over the past few years has the been the renewed interest in EGP, especially in the offset litho and flexographic packaging areas.
This recognises that the standard CMYK inks cannot reproduce some colours accurately; those vibrate greens, oranges and blues. At best, CMYK on a coated substrate can only match around 70% of Pantone colours.
This has resulted in the use of ‘special colour’ mixed to match Pantone and brand colour and printed on a 5th analogue printing unit. An expensive and time-consuming process.
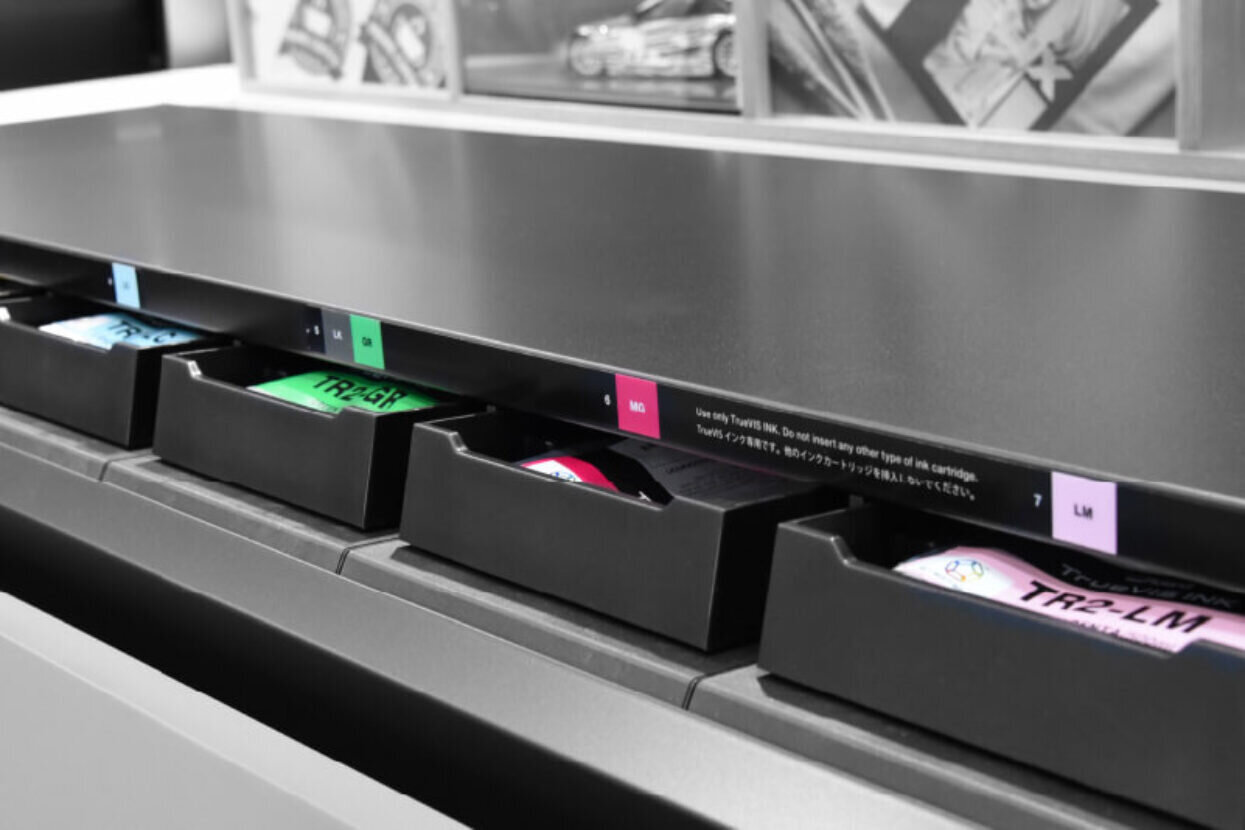
While there have been some attempts to introduce extra colours to the CMYK process over the last 290 years, Pantones Hexachome and Opaltone for instance, all have failed to gain market acceptance. This has many been due to the propriety nature of the products and limitation in the colour management and process control infrastructure at the time.
The latest implementations of EPP reflect the many advances in ICC colour management, process control and instrumentation in recent years. They allow the use of up to 3 extra colours, Orange, Green and Violet. This can increase the colour gamut by up to 25% and reproduce up to 90% of standard Pantone+Solid Coated colours. Some experts have proposed the use of Red, Blue and Yellow as the extra colours, but the consensus seems to be with the Orange, Green and Violet.
Software and standards
Some suppliers, such as Esko with their Equinox software, have software that will manage this EGP process, which is still many aimed at the packaging offset and flexographic analogue print markets.
Colour management software such as those from CGSOris, X -Rite, ColorLogic and Alwan support the creation of EGP profiles in 5, 6 and 7 colour profiles.
The CMYKOGV extended gamut process colour shave been standardised in ISO/TS 21328:2022. This is based on ISO 12647-2/2013 for the CMYK process control values.
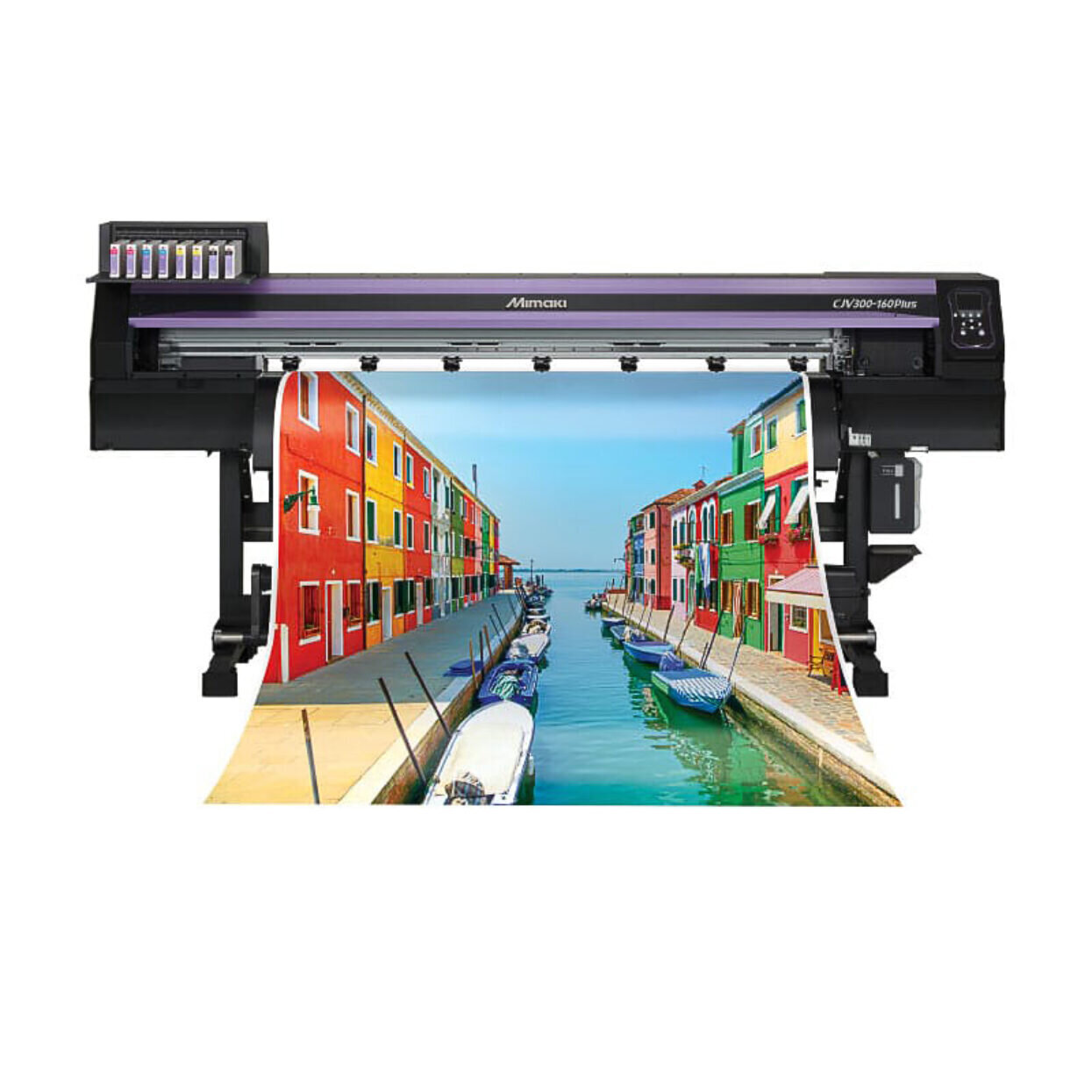
EGP and digital presses
As can be seen from the table below there are a wide range of differing sizes of CMYK+ colour gamut’s cover the analogue and digital printing methods. The smallest CMYK gamut for coated papers is often used a the ‘simulation’ profile in digital presses when the client needs to match offset litho output.
Comparative colour gamut’s on coated papers and boards | Gamut volumes |
Offset litho CMYK (Fogra 39/51) | 400,000 |
Offset litho CMYKOGV(Fogra 55) | 545,000 |
Toner digital press CMYK | 470,000 |
Continuous feed narrow web inkjet presses CMYK | 550,000 |
Wide format 12 colour inkjet press | 950,000 |
This then poses the question, ‘what relevance dos EGP have to wide format digital printing?’
While much of work will need to be produced to match a defined standard printing condition or ICC profile, many markets will benefit in using the wider colour gamut’s that some wide format digital presses offer.
The wide format 12 colour inkjet gamut referenced in the above table is one of largest in this market.
Every make and model will use a differing number and range of colour; from CMYK up to 12 colours. It should be noted that not all of the extra colour used are there to increase the size of the colour gamut. Light Cyans and Magentas are used to improve the smoothness of images and graphics, white and fluorescents are to provide special colours and effects. The colours used to increase colour gamut’s are usually orange, green and violet or red, green and blue.
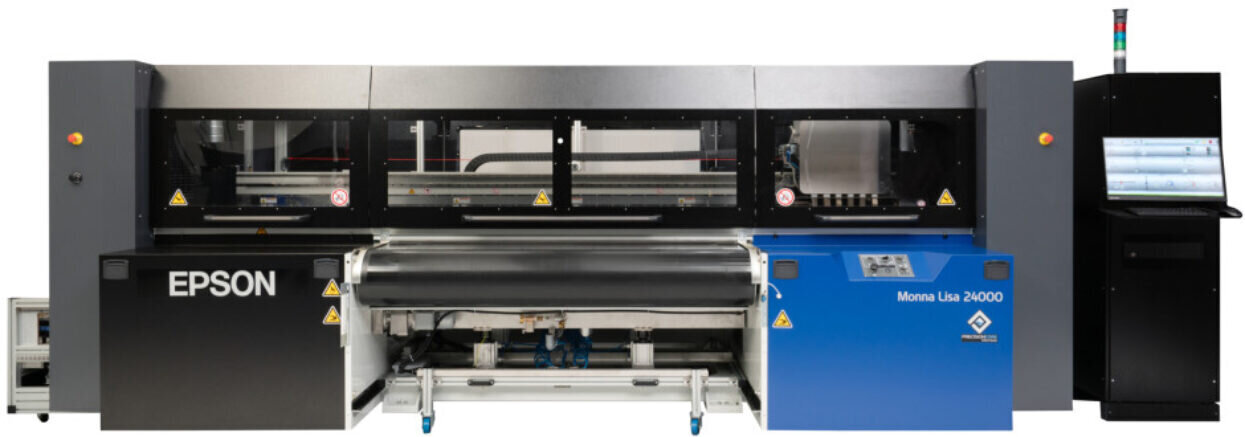
Some wide format presses may just offer or two of these extra colours to increase colour gamut.
If the intention is to run to the maximum gamut of the press and number of areas need to be considered.
- The maximum gamut of the press must be known for each substrate and a ICC device profile produced. There will be ICC profiles for a standard range of differing substrates installed in most digital fronts ends. These will not be as accurate as producing custom profiles for digital presses.
- Does the maximum colour gamut of the press offer any meaningful increase for the markets served.
- The colour managed workflows need to be addressed if the digital press using its maximum gamut.
- CMYK files and images supplied by clients will have probably reduced the gamut to a CMYK offset litho ICC profile. Using the maximum gamut of the digital press in this case may result in unacceptable colour results.
- A colour workflow from profiled RGB images is the best way to exploit the increased gamut of a digital press.
- Thought should be given to how and where the RGB files are converted the wide format digital presses device ICC profile. If the Digital Front End has good colour management controls, this can be done at processing/rendering within the DFE. Otherwise, the device ICC profile can be used in image editing and colour server software’s to convert the files to the profiles.
- If running a number of similar wide format presses, there may be an issue when using maximum colour gamut workflows. This can be addressed by comparing the device ICC profiles from each press and using the smallest as a simulation profile on the press with slightly larger gamut’s. Of course, if the colour gamut’s of presses vary widely, this will not be effective.
The term EGP can only really be applied to offset litho and other analogue printing methods. In the wide format digital area, the press and inks will control the maximum colour gamut of the press.
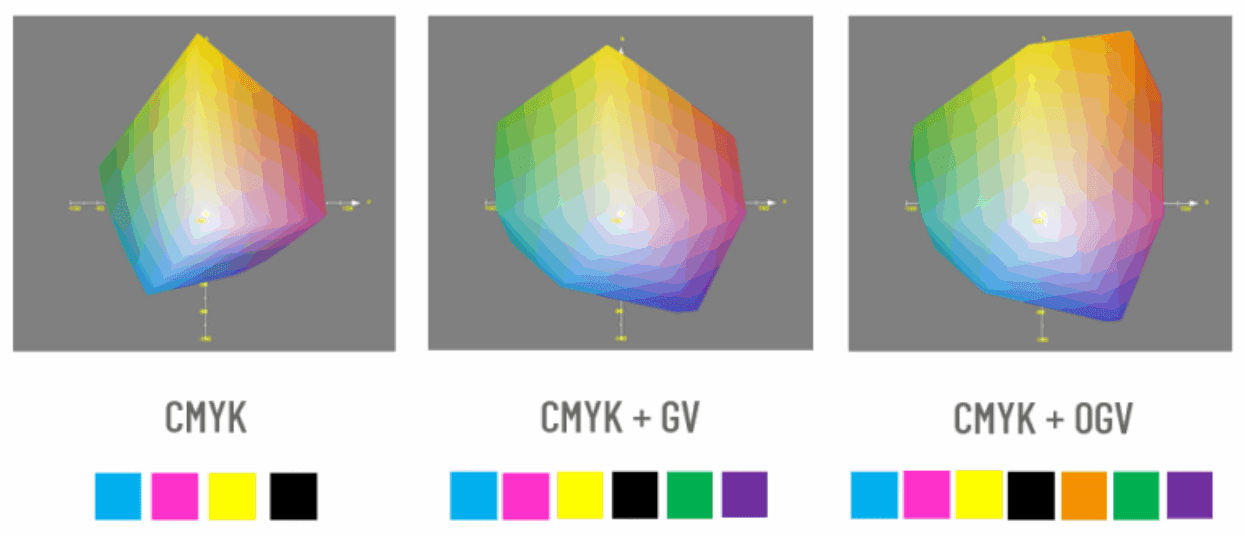
The better term for this in the wide format area is ‘Maximum Colour Gamut Printing’. This colour gamut on some wide format press can be over double the size of an offset litho press on coated papers, giving visually stunning results from RGB images.
The application of maximum gamut workflows will be market driven and will need close cooperation between the printer and their clients in order to achieve the best results.