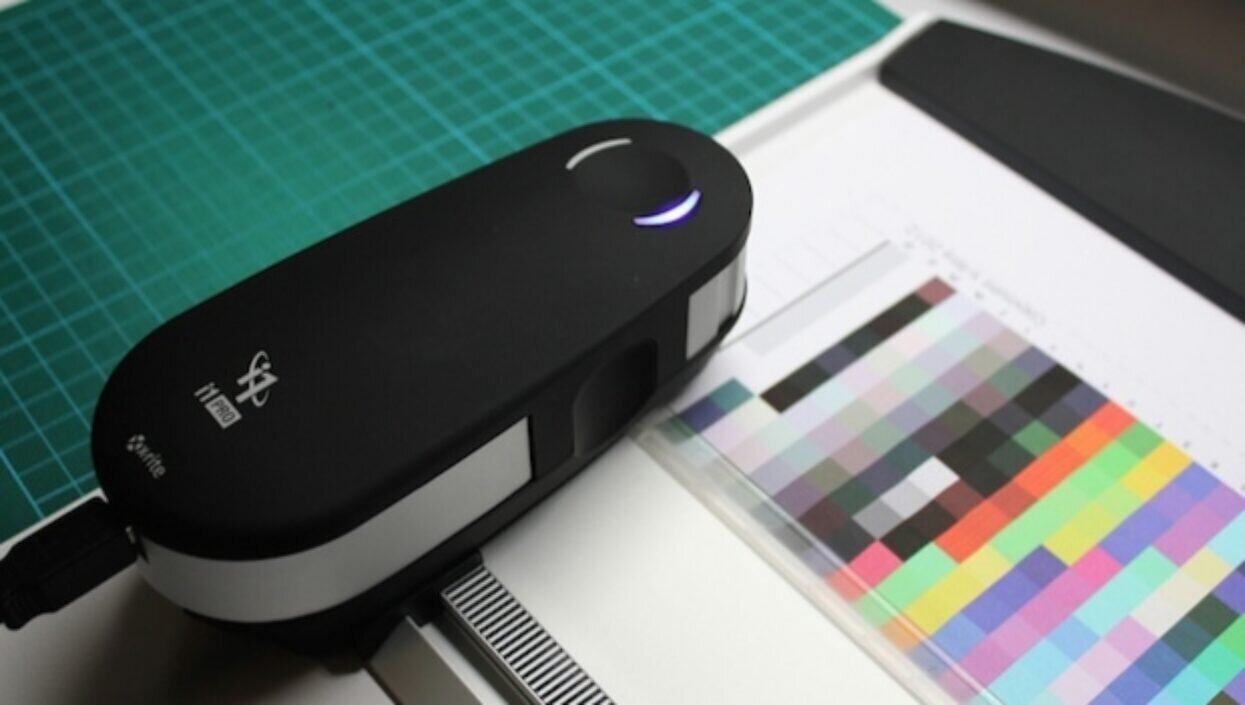
Fairly early on in digital imaging it was realised that we needed standards, not only for the image files themselves, but also for colour encoding.
There are several de facto standards for RGB images, such as sRGB developed in collaboration by HP and Microsoft, and then Adobe RGB. While sRGB has a relatively small colour gamut of around 700,000 colours, it’s often said to be a suitable colour space for images that are to be printed digitally.
Many printing systems have sRGB as the default colour space for incoming images in RGB, however for wide gamut printers sRGB is actually not the most suitable RGB colour space.
For photo-realistic printing the Adobe RGB is more suitable since it has not only a larger colour space in general, but it better matches the maximum colour gamut for offset litho on coated paper.
Characterization data for standardized printing conditions
Another de facto colour standard is the colour gamut of standardised litho offset, printed according the ISO 12647-2 standard. A very popular reference here is the FOGRA 39 colour data set which is used in many ICC profiles for standardised offset printing.
RGB images saved in Adobe RGB match the corresponding colours of CMY much better than sRGB, which has colour values for CMY quite far from the FOGRA 39 references.
But does it really matter you might ask? Can anyone really see the difference in the prints? Yes, very much so. A printing system is based on the Raster Image Processor (RIP) and a colour management system working in tandem.
If this system assumes sRGB for the incoming images in the data stream, but actually receives Adobe RGB, and doesn’t convert the colours properly, the resulting prints will look dull and colourless.
This is because the colour management system expected the smaller colour space of sRGB, and made its colour conversions from RGB to CMYK based on the wrong reference points. The numbers in RGB have different meanings in sRGB and Adobe RGB.
ICC colour management architecture
The reference colour encoding in modern colour management is the CIELab colour space. When converting from one colour space to another you need to look into the ICC profile associated with the particular image or printing condition, when performing the necessary colour conversions.
The International Colour Consortium (ICC) was founded in 1993 but still, after all these years, many prepress or press operators still struggle to get their heads around how to correctly manage colours, based on the use of ICC profiles.
This is especially true in wide format digital print production, despite the fact that applications often use expensive substrates and produce large images. However correct and precise colour management saves time and reduces waste and remakes. Deciding on which colour standards to set as your inhouse production standard is a sensible way to establish an efficient and profitable workflow.
In this sector there aren’t really any competing colour standards other than the use of ICC profiles. Making sure that the staff have a deep and proven knowledge of applied colour management, and that they understand how to use a spectrophotometer for colour quality control, is a good investment.
Colour tolerance in presswork
While densitometers are still of some value when measuring prints, they are actually colour blind because a densitometer measures the ink coverage. But it can’t really tell one similar colour from another. For this you need a spectrophotometer, and to decide on what tolerances for colour deviation are acceptable for you and your customers.
Colour deviation is presented as a value of Delta E (written ∆E). It’s generally accepted that the human eye can’t see a colour deviation smaller than ∆E 1. The next question will then be to decide how big a colour deviation is acceptable.
According to the ISO 12647-2 standard the answer is 5, and while this is a standard for litho offset, it can act as a guide also for wide format digital production. If the print buyer insists that a specific corporate or brand colour should be defined and printed as a spot colour, then a slightly tighter tolerance might be applied, for example ∆E 2.5.
Using standards in colour management and defining tolerances will save you time, reduce waste and perhaps even more importantly, improve customer satisfaction and goodwill for your business.