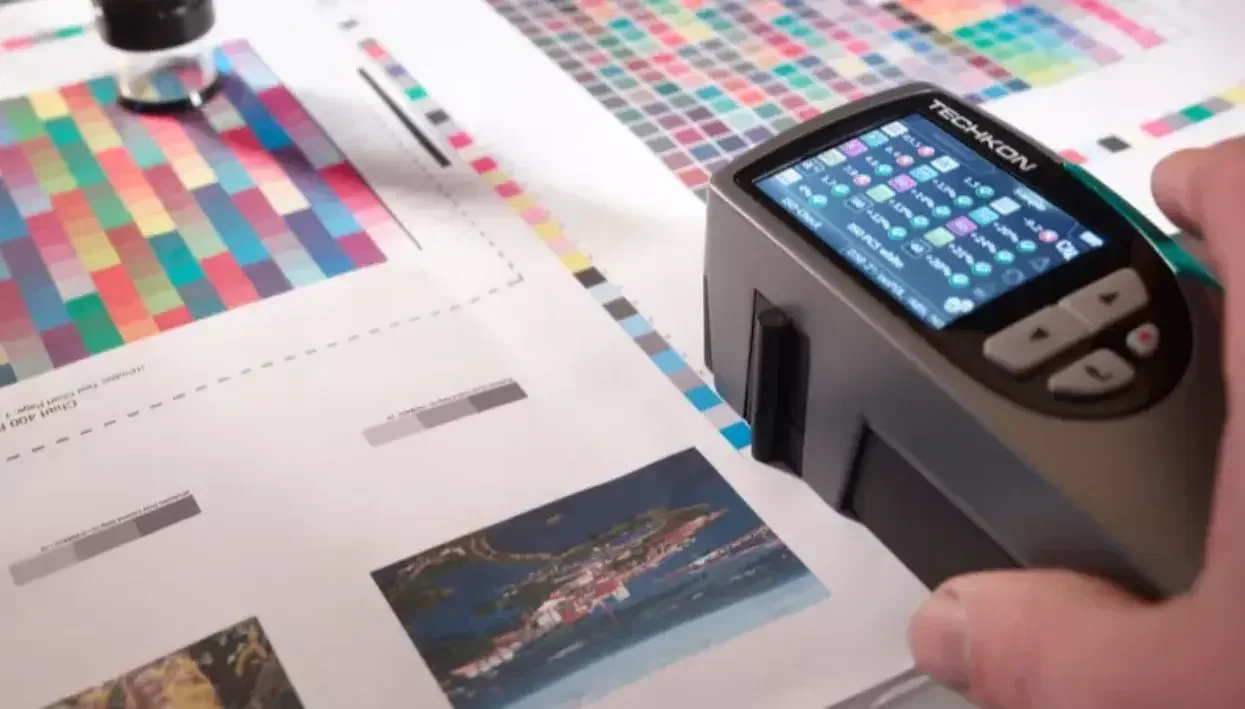
At the recent Fespa Expo in Munich, process control was part of the Fespa Colour LAB and was included in the tour of feature. This seemed to be a new concept to many visitors. This blog with give a little more detail as to where it fits into a colour managed system and workflows.
In this instance, process control as term is used to refer to the printed product validation and verification, rather than the wider meaning within the quality assurance area, when using standards such as ISO 9001.
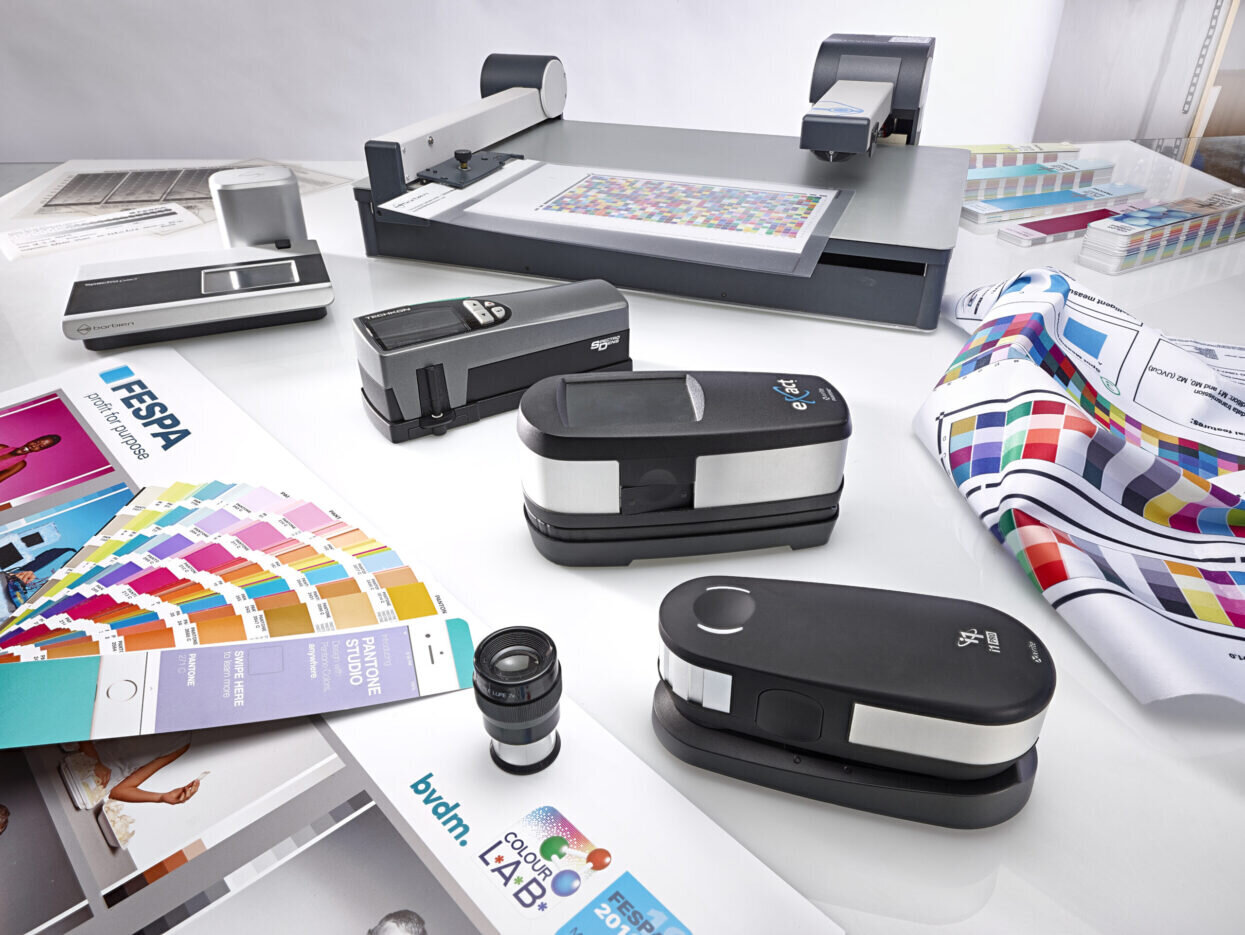
See the blogs on Club Fespa from Paul Lindström…
So, your colour managed workflow is complete:
- Profiled and verified computer screens to view images and pages accurately
- The printing conditions chosen for your presses to emulate, Fogra 39, 47, 51, 52, or even the CMYK full gamut of press, etc
- Color settings files in desktop apps that reflect your colour workflows producing press ready PDF X files
- Clients advised on how to submit press ready PDF’s to the correct colour managed workflow
- Presses are device profiled for the many substrate’s used
- The RIPs /DFE’s driving the presses have their colour management tools set up to match the chosen printing conditions using the correct simulation ICC profile in combination with the device profile for the presses/substrate combination
There are many software solutions available including PressSIGN from Bodoni (now owned by Agfa, their version is called PressTune and there is also a version for digital print called PrintTune). ColorCert from X-Rite, PrintSpec from MellowColor, PressView from MeasureColor, EFI Fiery Color Verifier, Techkon’s SpectroConnect and on-press/in-line systems for digital and offset litho presses.
These solutions can use small colour bars which suit work where there is little room for a large colour bar.
So, what is needed in the digital wide format printing sector to enable process control?

For large format work, often a Fogra Media Wedge, see above, can be used and measured using the same process as used for validating proofs.
However often there is a need for smaller colour bars, such as the small PressSIGN bar or one of the Fogra bars shown below.

The number of sheets/products sampled and measured will be based on the run length, clients may set this figure, some print certification schemes, such as the UK’s BPIF Colour Quality Scheme mandate the number of sheets measured in relation to the run length.
Often for very short runs, say up to 10 copies, only one measurement of one copy may be needed. For longer runs a sampled will need to be assessed in relation the stability of the process and client needs.
The sheets with be measured either by inline spectrophotometers which are on some wide format inkjet devices, or off-line using a handheld spectrophotometer and process control software.
Even this more manual approach only takes a minute or two.
These systems take the intended printing condition, which can be an ISO standard or the chosen simulation ICC profile. They measure the colour bar and report the accuracy in De.
The measurements usually cover:
- CMYK primaries
- RGB overprints
- Grey balance
- Dot gain, in the digital world this is using the colorimetric values of usually three tint areas to check against
- Paper or substrate white point
These measurements and scores can then be recorded ‘job-by-job’ and stored in a database.
They can be used for monitoring press performance and KPI‘s for colour control. They will show very quickly when a press needs a new device profile or calibration. They can be provided to clients to prove colour accuracy and consistency for a project or individual job.
The investment needed is not large. It some cases the digital front end used to drive your wide format presses may have a process control tool, usually in this case, using a Fogra Media Wedge. Also, often a spectrophotometer, such a as a X Rite iOnePro, will be supplied with the press in order to produce device profiles and calibration.
This, and other spectrophotometers, will work with the process control software’s and systems mentioned above.
These process control software’s are not expensive, ranging from 2500 euros for a single user to 8,000 for a multiuser server-based system. Most will run on Mac or PC.
So, what benefits will be achieved by using these systems other than mentioned above?
- Printed work can be measured and verified to an agreed and known specification or standard
- This then can be shared with clients
- Less wastage and reprints due to poor colour
- Provides diagnostic data on press performance, in order to correct colour issues before they effect quality
- Greater customer satisfaction and confidence