With print and cut machines becoming increasingly common in print workshops around the world, FESPA.com takes a closer look at this technology and picks out the key benefits to users.
Traditionally, printing and cutting had been viewed as two separate parts of the production process, with the initial printing taking place on one machine before the job was moved forward to be cut and finished.
However, the influx of print and cut technology in recent years means that print service providers are now able to save time by carrying out both processes on a single device. Such has been the success of this kit that some of the top brands across the market have released their own versions.
With this in mind, FESPA.com looks at some of the latest developments in the print and cut market, highlighting some of the main benefits for users and how they can use this kit to enhance their service offering.
Very sensible business investment
One of the leading names active in the print and cut market is Roland DG, which has a number of solutions on offer. Rob Goleniowski, head of sales for UK and Ireland at Roland DG, said that the versatility alone of print and cut machinery makes a strong case for this type of technology.
“With a single device, you can print and kiss-cut/perf-cut a wide range of materials which unlocks a whole catalogue of new products, from bumper stickers to custom t-shirts and even packaging prototypes,” Goleniowski said.
“There are other benefits that stem from the simple fact that you only need one device instead of two – it’s a smaller initial investment, it takes up less space and without the need to move media between devices, it’s less labour-intensive and easier to use.
“Following on from that point, since the media can remain in place for both print and cut operations, this technology enables unattended production, even overnight. Put all these benefits together and you have a very sensible business investment.”
Looking at the Roland DG portfolio of print and cut machinery, Goleniowski pointed to the recently upgraded TrueVIS VG2 solution as one solution for print companies to consider. Goleniowski said the device has been designed to offer industry-beating quality to businesses of all sizes, regardless of their budget.
“We’ve taken a comprehensive approach in developing this solution, focusing on the speed, build quality and reliability of the hardware, the colour output and range of the new TR2 ink, and the usability and power of our VersaWorks 6 RIP software,” Goleniowski said.
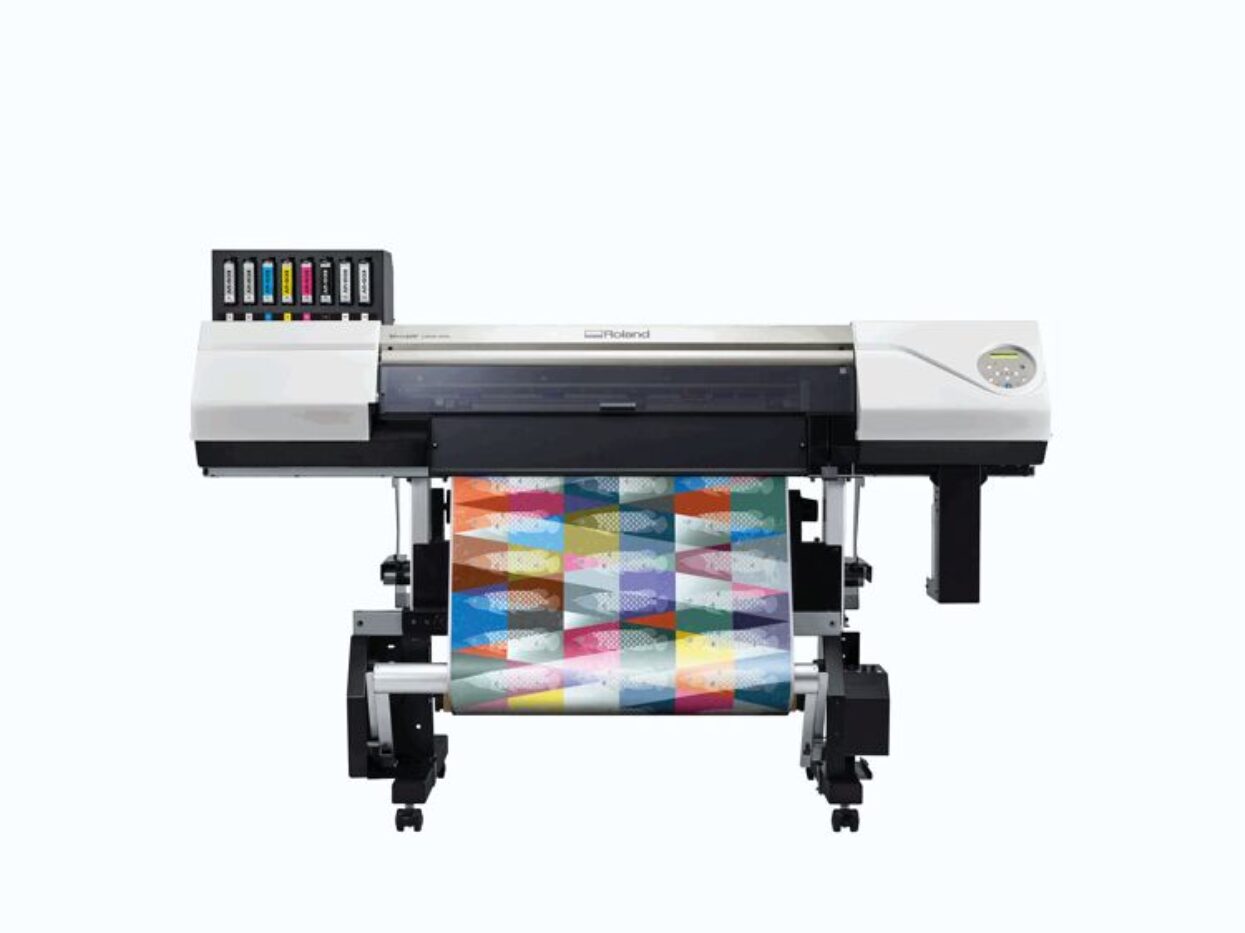
Caption: Roland DG’s new VersaUV LEC2-300 has a clear ink that allows users to add value to their products with special effects, textures and features such as simulated embossing, highlighting and Braille.
For print companies looking to go down the UV printing route, Roland DG’s new VersaUV LEC2-300 is billed by Goleniowski as a technological leap forward from its predecessor, the LEC series, and at a lower price.
“This solution offers instant ink curing, superb print quality and speeds that can keep up with the most demanding production queues,” Goleniowski said. “Furthermore, the clear ink lets users add value to their products with special effects, textures and features like simulated embossing, highlighting and even Braille.”
Identifying the right solution for your business
Elsewhere and HP is also able to offer solutions to print companies in this area. Michael Lewis, Latex account manager at HP, said that combining high-quality wide-format print with super-accurate digital cutting can open up “exciting new avenues for a range of businesses” in the market.
Lewis said: “Like any equipment investment, print companies need to find the print and cut solution to meet their individual needs. There are combination printer-cutter systems on the market but many users may find a separate a printer and cutter set-up more appropriate.
“For instance, businesses that typically produce one type of application in high volumes that require little cutting may want to invest in a high-specification production printer but an entry-level cutting system. Or, a business that uses two or more printing technologies – dye sublimation for textiles and Latex for signage, for example – may be able to use one cutting system in both workflows.
“In addition, a separate printer and cutter can work on two different tasks simultaneously, which an integrated machine cannot do. This is ideal for fast-moving production rooms with operators working on multiple projects at one time. Every business is different so it’s essential to have options.”
Looking at the technology available from HP, Lewis pointed to the HP Latex print and cut solution, which comprises four components designed to be integrated together for a seamless workflow.
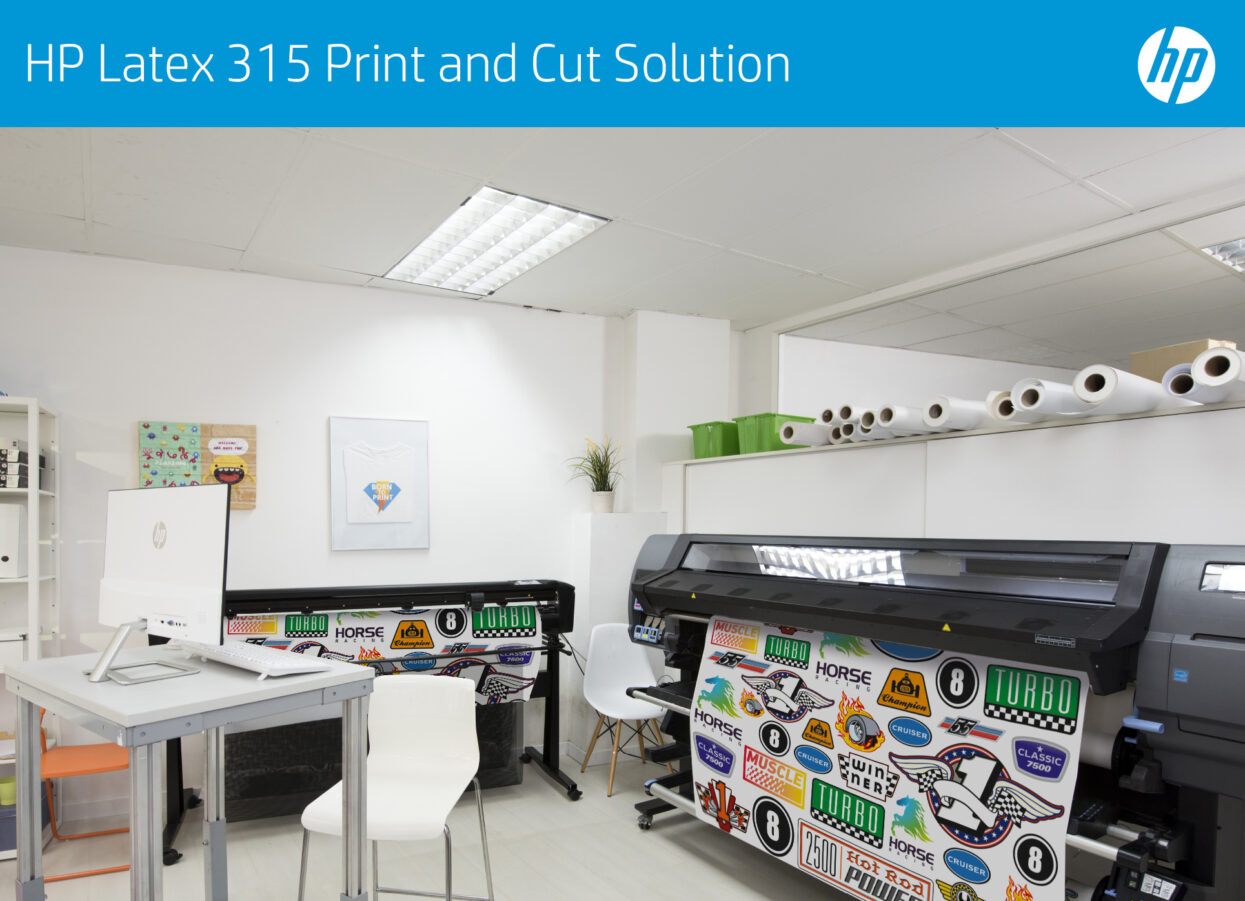
Caption: According to HP, its Latex 335 Print and Cut solution can help print companies to expand into larger applications with a 1.63m width.
The HP Latex 315 Print and Cut solution, which features a business-ready 1.37m printer option, while the HP Latex 335 Print and Cut solution, Lewis said, helps users to expand into larger applications with a 1.63m width.
Lewis said: “HP Latex is renowned for its exceptional printing quality across an incredible variety of substrates using ecologically sensitive, odourless water-based inks. There’s no need to wait for de-gassing or lamination so prints can go straight onto the HP cutter, designed in partnership with globally respected, high-quality cutter manufacturer Summa.”
The cutter uses the HP Barcode system to achieve the right registration and accurate cutting, while the print-and-cut solution is connected using the open-architecture HP FlexiPRINT and CUT RIP software, making both printing and cutting steps quick and simple for operators, Lewis said.
The fourth element is a selection of cloud-based applications that are accessible to both the user and their customers, enabling them to design and send files to the FlexiPRINT software remotely.
Lewis added: “Businesses around the world use this true print and cut solution to produce incredible work, efficiently and profitably.”
Low investment and saving space
Another market leader championing the use of print and cut devices is Mimaki, which has a number of its own solutions available to companies all around the world. Senior product manager Bert Benckhuysen said that one of the major benefits of print and cut machines is the low investment cost associated with this technology.
Benckhuysen said: “You can print and cut with one machine, as opposed to buying a printing machine and a cutting plotter. A combined print and cut machine also saves floor space and enables unattended print-and-cut jobs. You can just set up the job, leave to work on something else while it is running, and come back when it is completed.
“Compare this with having two separate machines: after the printing job is complete, someone needs to manually set the roll on the other machine for cutting.”
Looking more closely at the machinery that Mimaki has on offer in this area and Benckhuysen highlighted the manufacturer’s most recent release in the form of the CJV300-160 Plus. This solvent print and cut machine is equipped with the latest version of Mimaki’s anti-banding technology – the Mimaki Advanced Pass System (MAPS) – that helps maintain high image quality even at higher print speeds.
The CJV300-160 Plus also features the new ID Cut function that Benckhuysen said will help to ensure a more efficient print and cut operation, as well as the new reusable eco ink-pack for increased production efficiency and reduced ink costs.
Apart from the CJV300 Plus, Mimaki also offers the UCJV300 Series, a range of combined print and cut machines with UV LED print technology. This product range is also equipped with Mimaki’s latest core technologies such as MAPS and ID Cut function, but with the added benefits of UV LED print technology.
Other benefits of the UCJV300 Series include the capability for users to print on a wider range of materials, the fact that the print result is immediately dry and ready for post-processing, thus saving time, while it has less power consumption and does not use any Volatile Organic Compounds (VOCs).
From speaking with some of the leading brands in this area of the market, it is apparent that print companies can expect a number of major benefits from investing in a print and cut device. From saving space in the workspace, to reducing the cost of having to purchase more than one piece of kit, there are plenty of positive factors to focus on in this area.
Roland DG, Mimaki and HP will be exhibiting at the FESPA Global Print Expo 2020 from 6th – 8th October 2020 at the IFEMA exhibition centre in Madrid. The Global Print Expo 2020 will be the meeting place for the industry to connect with over 700 exhibitors, showcasing their product innovations and demonstrating their solutions for screen and digital wide format print, textile printing and signage. Once registration is live use Promo Code FESH201