Robotic solutions, particularly cobots, are increasingly prevalent in the printing industry, especially in wide format. They excel at repetitive tasks like loading/unloading presses and cutting tables, boosting productivity and safety. Key players like Agfa, Durst, and Zund offer integrated systems. While initial investment and programming are significant, falling costs and improved integration make robotics crucial for automating physical workflows in print factories.
One of the most striking features from recent Fespa trade shows has been the growing number of robotic solutions, both small and large, used mainly with presses but also for cutting tables. This is part of a wider trend towards automation to improve productivity.
Robots are extremely good at repetitive tasks such as placing boards or sheets onto a flatbed and then moving them onto a palette once printed. They don’t need to take a break or a holiday and can easily cope with moving a thousand boards or more per hour. There’s also a good health and safety argument for making greater use of robots, as they can carry heavy weights with no risk of dropping something on their feet or straining their back muscles.
Robots come in many different sizes, shapes and configurations from home vacuum cleaners to interplanetary landers. Essentially they are machines equipped with sensors that carry out computations to make decisions and perform actions.
Most of the robotic solutions that you can see at Fespa shows are more accurately described as collaborative robots or cobots. They are designed to work on the factory floor alongside people and use sensors to detect humans and avoid accidents. Most of those used in printing are robotic arms, bolted to a fixed position to allow them to handle heavy weights.
Robotic solutions are appearing throughout the printing industry, for various uses such as loading plate cylinders on flexo presses, placing book blocks in binding lines or moving palettes of paper to B1 offset presses. In wide format they are most commonly used for loading and unloading boards and sheets from flatbed and hybrid presses.
These robotic arms are limited to certain movements, or axis. Most wide format printing will need six axis of movements. In theory, five axis is enough for picking the substrates up, rotating them, moving them from palette to bed and placing them back down again. But if you also want to be able to flip the sheets over to print on the reverse side then you’ll need the sixth axis.
With most hybrid printers you are going to need separate solutions, with one robot loading, and another unloading on the other side. You should also consider the full workflow. It might be more efficient to have a cutting table next to the printer, and for one robot to move the printed boards direct from the printer to the cutting table. Careful placement might also allow you to have the same robot take the printed boards off the press and deposit them on a palette, and then go back and move those boards from palette to cutting table when needed.
Equally, however, you could use robotic palette movers to deliver a palette load of media to the press, and then to take a stack of finished boards to whatever the next finishing process is. Depending on the gripper head in use, they can be used with cutting tables to pick up the items that have been cut out, leaving the waste to be dropped into a bin from a conveyor.
Robotics in use
Inca Digital, now owned by Agfa, has long been a proponent of using robotics to automate the loading and unloading. Agfa has embraced this since acquiring Inca, showing off twin robots, which it calls Max Bots, for fully automated loading for its Tauro XUHS at the recent Fespa Global show in Berlin, as well as on the latest generation of the Onset Panthera flatbed.
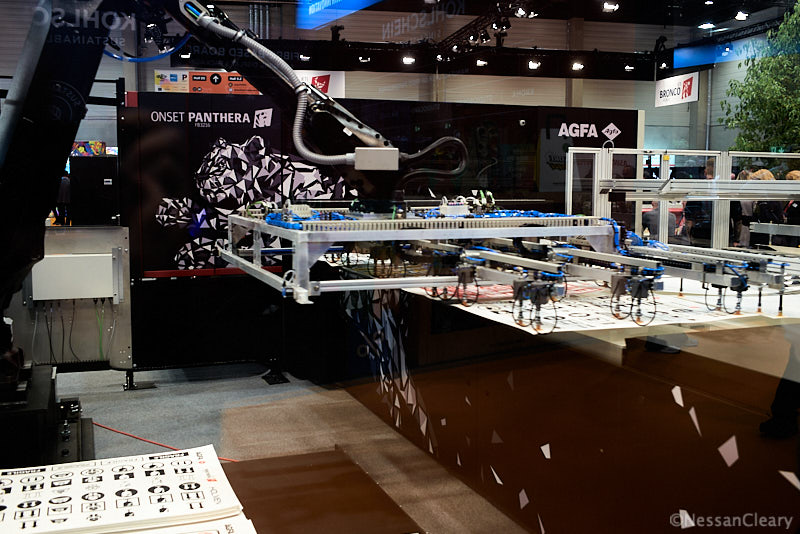
Durst also has developed a robotic solution for its P5 family of wide format hybrid presses. These are mainly used with the P5 350 HS printer, which has the print speed to benefit from the robotic boost to productivity and therefore to justify the investment cost. The full solution involves two robots either side of the printer, one for feeding and one for stacking printed jobs.
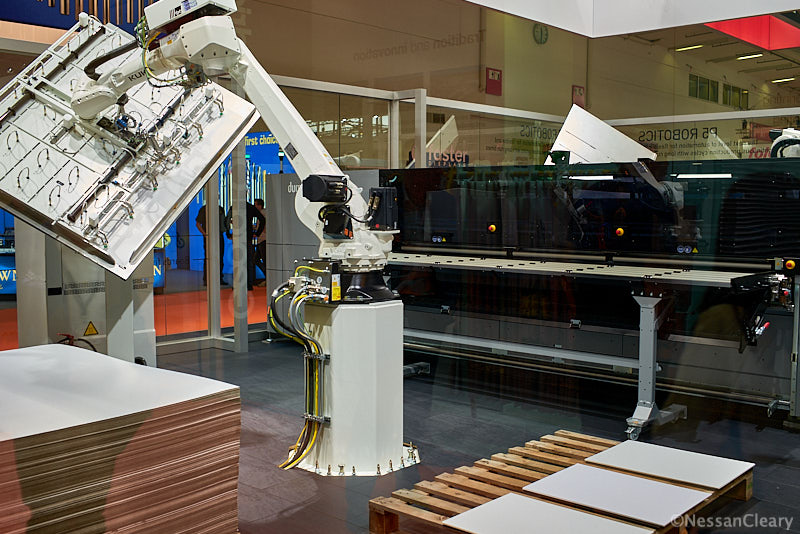
The system includes an angled registration station on the side so the robot picks up the sheet from the stack, drops it onto the station and picks it up again, this time knowing exactly where the board is so that it can then place it in exactly the right position on the printer. This mechanical approach to registration enables it to handle thin materials like foil paper as well as cardboard and is faster and more accurate than using a sensor.
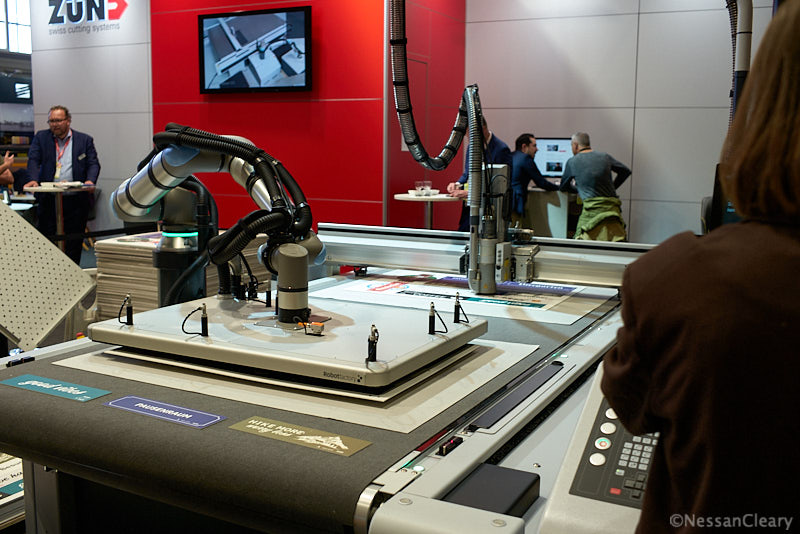
Zund has partnered with the Danish firm RobotFactory, which develops both standard and customized robot handling solutions. These can be used for loading but also for picking and packing finished objects. As well as industrial robots, RobotFactory also supplies smaller systems, called PortaTables, designed for quick and easy deployment.
Integration and servicing
There are a number of factors that customers should consider. The most obvious of these is the degree of integration needed. In theory, there is nothing to stop a print service provider from working directly with a robotics company and setting up their own automatic loading/ unloading solution. But in practice this is probably best done through the press vendor in order to integrate with their systems, without voiding their warranty. Besides, the press vendors will also have the expertise required for separating and handling the wide range of substrates that most print companies will be using.
These are industrial machines and should be capable of a very long service life. This may be longer than the life of the printer so you should also consider how to repurpose the robots to work with other presses in the future, and who will pick up the cost of any further integration work. You will also need a separate service contract for the robotic solution.
In conclusion, robots are expensive to implement, mainly because of the degree of programming that is required. But as they become more widespread and vendors learn how to better integrate them, then the costs will fall. More importantly, with automation having already tightened up the way that job files move through production, the next major bottleneck is how those jobs physically move through the print factory, from blank media to finished items.