Corrugated targeted as the next digital domain
Digital corrugated printing finally seems to be taking off properly after a couple of false starts in the last decade, Simon Eccles finds out more.
More and more large format presses are appearing that have been designed or modified for high speed printing on corrugated paper and board for large format display work as well as boxes and containers. While there has only been a handful of installations so far, these systems target a predicted emerging demand for shorter runs and shorter lead times, with the additional facility to localise or personalise the printed images.
Corrugated packaging and display materials are a versatile medium that can act as strong enclosures for end-of-aisle product promotions, that incorporates large printable areas for promotion of the contents. White lined corrugated material can present an attractive surface for print, with the option of coatings up to high gloss. Other possibilities are general POS signage and cutout stands, personalised or localised promotional boxes for heavy by high value goods (such as whisky bottles), and of course, general packaging containers.
Companies that have recently announced systems or development programmes already include Barberan, Bobst, Durst, Fujifilm/Inca, HP, Sun Automation and Xanté. They are targeting a sector that mostly uses flexography, lithography or screen printing today. They all use inkjet technologies and most of them are priced at well over 1 million euros, reflecting the complexity of their materials handling systems as much as the speed of their print engines. However Xanté has taken a simplified route to produce its manually fed €75,500 Excelagraphix 4200P.
The technologies divide into water based or UV cured inks, and single or multiple pass heads. Single-pass has the highest speed potential, although multi-pass may still have the edge in image quality.
Sean Moloney, product manager for Sun Automation’s CorrStream, says that wide format single-pass printers will change the whole economics of short to medium runs: “Sun, Barberan and Bobst fall into this new category of high speed wide format printers. Speeds are in excess of 4,000m2 per hour and these are in line with analogue outputs. We have uptimes in excess of 80%, which is more than flexo, so we are very productive. Standard litho and flexo presses struggle to get to 50% due to make-readies on shorter runs.”
“Printers will be looking at ways to reduce their running costs when producing signage in up to 200, 250 units, which is typical of what you’ll see going through the average Durst, HP or Inca,” he said. “What we’re presenting is a way to produce those with just as good a quality, colour and gamut, but with a single pass technique. This gives four or five times the output speeds, which by definition reduces your costs.”
The idea of digital corrugated boxes or display printing isn't new, but it’s suffered a few false starts over the past decade, partly because the ink and printer technology wasn’t ready, but also because the market wasn’t either.
Apart from the challenge of persuading large format high speed inkjet printers to work on an often dusty substrate, there are materials handling issues too. Corrugated materials aren’t very rigid and there’s a particular danger that they may buckle and strike the print heads, which damages them.
Feeding is an issue too: not so much with rolls, but large format display boards are both comparatively heavy and not particularly rigid over large areas. Hand pre-feeding with “3/4 automation” loaders limits the throughput speed, so a fully automated fast feeder is desirable for the really fast models. These are expensive to build and occupy a lot of space.
Single pass speed
An early attempt to build a very high speed corrugated inkjet came in the mid-2000s when UK’s Inca Digital was commissioned by Sun Chemical to develop a 1,040 mm wide single-pass corrugated sheet fed press with UV inks. Named FastJet, it was intended for speeds up to 100m per minute and needed nitrogen bed assistance to cure the ink at those speeds. Only three were made and none are still in operation.
However, its legacy has recently re-emerged. Sun Automation, a US based manufacturer which is unconnected with Sun Chemical despite the name, developed part of the materials handling system for FastJet.
It has recently launched a family of single-pass high speed corrugated sheet fed presses of its own, called CorrStream, which all run at 70m per minute with aqueous inks. This is equivalent to 4,500 1m2 boards per hour, the company says. The widest model will run at a little over 5,000m2 per hour.
There are three different widths, the Corrstream 20, with a maximum width of 537mm, has a list price of €1.6million. The 40 has a width of 785mm and a price of €2.1m, while the 66 has a width of 1,345mm and will be priced between €3.1 and €3.3 million depending on configuration. However, leasing arrangements are more likely.
One has been installed already, at a so-far undisclosed location in the southern USA. A demonstration machine has been running in the company’s UK site in Bristol, UK, since April. Sean Moloney Sun Automation’s product manager for Corrstream, said that the main sales effort this year will be on Europe.
“We’re showing boxmakers and converters of any corrugated substrates how to reduce costs on a like-for-like basis, so they can bring across work and we can show them that they can print it more cost effectively than they can now,” he said. “The second part is to show them how they can print variations and on-demand, reduced inventories, reduced lead times, so they can generate more value in the product itself. We can do both and we prove them time and again with large jobs.”
He said the company originally tried developing a corrugated press based on Kodak’s Prosper continuous inkjet heads, but gave up in favour of a so far undisclosed drop-on-demand head array. The company’s major experience is in corrugated feeders, especially its front edge feeder which Moloney says is the key to Corrstream’s materials handling.
“We have the same length and width as an HP 15000 (pictured below) but we run seven times faster,” he claims. “We generate the same sort of print quality on uncoated substrates. Our machine may be double the price, but it gives four or five times more print.”
The HP 15000 Corrugated Press uses fast multi-pass heads and an enhanced feed and vacuum system.
Spanish industrial printer manufacturer Barberan is shipping a corrugated version of its UV sheet fed presses, also used for laminates, decorative papers and the like. The 1.26m wide Jetmaster BIJB-1260 is the widest of the Jetmaster range and can print on corrugated sheets up to 51m per hour, equivalent to 4,100m2 per hour. Its resolution is 360dpi, with three grey levels from the printheads to increase perceived quality. For corrugated it has a pile feeder and a delivery conveyor leading to a stacker.
In 2013 Bobst made a joint announcement with Kodak, saying it was developing a fast corrugated single-sheet fed press based on the Kodak Prosper S-series continuous inkjets. This will use a water-based ink. Bobst has said very little since apart from a brief update at June’s FEFCO summit in Brussels, but it may be launched in 2015 or 2016.
A rather different solution was recently announced by HP. The High Speed Corrugated Solution is based on a simplex configuration of its T400 inkjet web press. This is not a direct digital corrugated printer, instead it pre-prints white liner paper that is later combined with the other layers on a separate corrugating machine. It prints on media up to 1,066mm wide at up to 182m per minute (12,000m2 per hour), using aqueous inks. Price is around 3m.
Hand fed alternative
You don’t have to pay more than a million for single-pass corrugated. The compact €75,500 Xanté Excelagraphix 4200P is also a single pass sheet fed printer, but built for hand feeding at much more modest speeds. It uses a 1066 mm wide Memjet printhead array with aqueous dye inks, for speeds up to 18 metres per minute at 1,600 x 800 dpi (or half that at 1,600 x 1,600 dpi). It can accept heavy corrugated and foam boards up to 1,066 x 2.500mm.
European general manager Melissa van Gelderan says that the current sales focus is on box making rather than display, as that represents a larger initial market. Some 50 have been sold worldwide since shipping started about a year ago.
Multi-pass heads
Other corrugated digital models on the market or under development are multi-pass machines, essentially modified flatbed industrial printers that have been given semi or full automatic board loaders and unloaders. The automation costs a lot, so hand feeding might be more attractive in in low labour cost markets.
The first inkjet press built for corrugated was an aqueous ink sheet fed multi-pass press originally developed by Aprion in Israel. Aprion merged with Scitex’s large format operations to become Scitex Vision before being taken over to become HP Scitex. The latter company brought it to market as the CORjet FB6700 in 2006. Indirect descendants are the UV cured FB7500 and current FB7600 flatbed, which can handle corrugated board, paper, foam board, Dibond and plastics on sheets of up to 1,650 x 3,200mm.
Earlier this year HP introduced a dedicated corrugated version of its fast general-purpose FB10000 flatbed, called the 15000 Corrugated Press. This takes sheets up to 1.6 x 3.2m and can print about 500 sheets per hour with auto loading and unloading. It announced the first sale at FESPA Digital in Munich this year, to Image Factory in the UK, which already had an FB10000 that it uses for POS display work on corrugated and solid media.
In 15000 configuration with a stack loader you get multiple droplet size HDR (high dynamic range) printing at speeds up to 500m2 per hour on 1.6 x 3.2m sheets for POP work, or 600m2 some for other work. Up to four sheets can be loaded and printed side by side with the autoloader, though manual loading is possible too.
“It’s definitely targeting primarily display, and secondarily packaging,” said Amir Shalev, HP’s product marketing manager who specialises in corrugated. “We are reaching a print quality that’s good enough to match what was in the past laminated. We see a major opportunity in short run lengths of a few hundred units. When you have a retail company like Tesco in the UK or others in the USA, with a typical run length for display being between 300 and 700 copies. Each unit can be made out of different pieces, say four.
“So your economical break even point would be justified by these type of machines. Some machines we see now, such as Sun Automation and others, are taking about higher speeds. But the images coming out of them in my opinion are not really good enough to target laminated display work. They're more targeting basic flexo packaging.”
Durst has been building corrugated sheet fed models with multiple-pass heads for some years. Its current Rho 1000 Corrugated (pictured below) is a UV flatbed with a 2.5 m width, able to print up to 1,000m2 per hour at up to 600dpi. Unusually it has the option for more than four colours: apart from CMYK, light cyan and light magenta, there are options for gamut-extending orange and green or green and violet.
Although Inca Digital no longer makes the FastJet, it is still linked to corrugated though its fast but multi-pass Onset S40i. A robotic system was commissioned by Fujifilm to automate the loading and unloading of large format corrugated boards up to 3.14 x 1.6 metres in size. Fujifilm markets and sells the Inca Onset models worldwide. In addition Fujifilm, Speciality Inks (the former Sericol), has developed UviJet OC, a paperboard-only version of the Onset ink that costs less as it doesn’t need to adhere to plastics.
Expansion opportunities?
It’s easy to regard corrugated as the domain of packaging converters, but as we’ve seen, there’s a lot of potential in display and POS work, especially if the economics shift in favour of just-in-time and personalised work.
Corrugated packaging converters who use flexography almost all use outside platemakers, so don’t tend to have inhouse experience with pre-press workflows. On the other hand companies that already have experience in large format inkjet for sign and display, are used to pre-press already and will usually have some form of relevant workflow set up. They could find it a relatively easy move into large format corrugated for display, and from there into packaging ahead of the flexo converters, if they see a market opportunity.
Topics
Interested in joining our community?
Enquire today about joining your local FESPA Association or FESPA Direct
Recent news
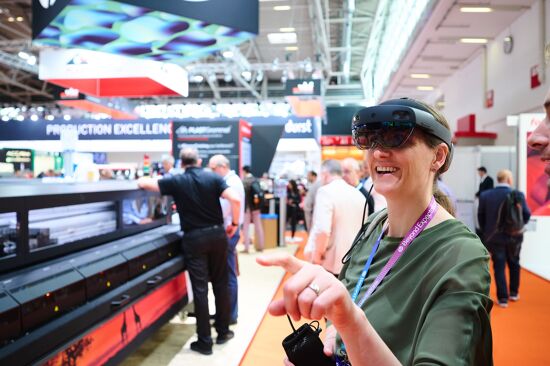
Streamlining personalisation with tech: Insights from the SmartHub Conference 2025 speakers
Personalisation Experience 2025 (6 – 9 May 2025, Messe Berlin, Germany) is running its inaugural SmartHub Conference from 6 – 8 May 2025.
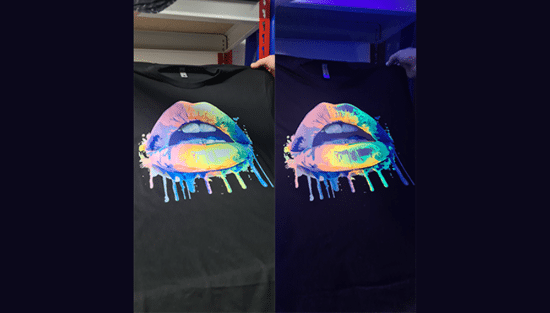
Special Effects in DTF: How Neon Inks Are Making Apparel Pop
Neon fluorescent inks are the latest innovation in DTF printing, offering vibrant, eye-catching effects under both daylight and UV light, giving apparel decorators a competitive edge. Testing shows good wash durability, though market perception of added value is still developing. With increasing adoption and ongoing technological advancements, neon represents a significant upgrade for creative customisation.
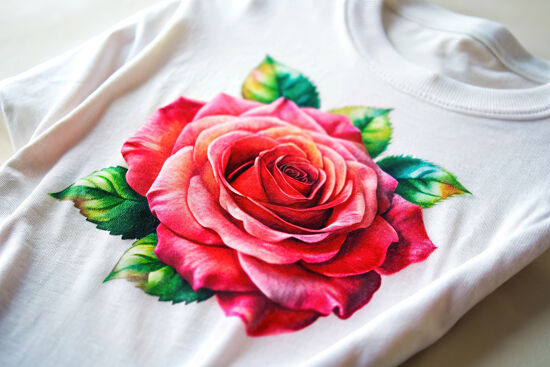
Unlocking Growth Opportunities in the Printed Personalised Apparel Industry
The printed personalised apparel industry is booming, projected to reach $10.1 billion by 2030. Driven by consumer desire for self-expression and branding needs, technological advancements like DTG/DTF and e-commerce integration are key. Sustainability, eco-friendly materials, and on-demand printing are crucial growth drivers. Businesses leveraging these trends, including AI and social media, have significant commercial potential.

Personalisation: From mass production to print-on-demand
Technological advancements are driving the growing trend of personalisation, fueled by consumer demand for unique products. From packaging campaigns like Share-a-Coke to customised apparel by Nike and Adidas, and AI-powered tools, the shift from mass production to print-on-demand is evident. The SmartHub Conference at the Personalisation Experience from 6 - 8 May will explore these opportunities and challenges for businesses.