Are bio-based synthetics a solution to the climate crisis?
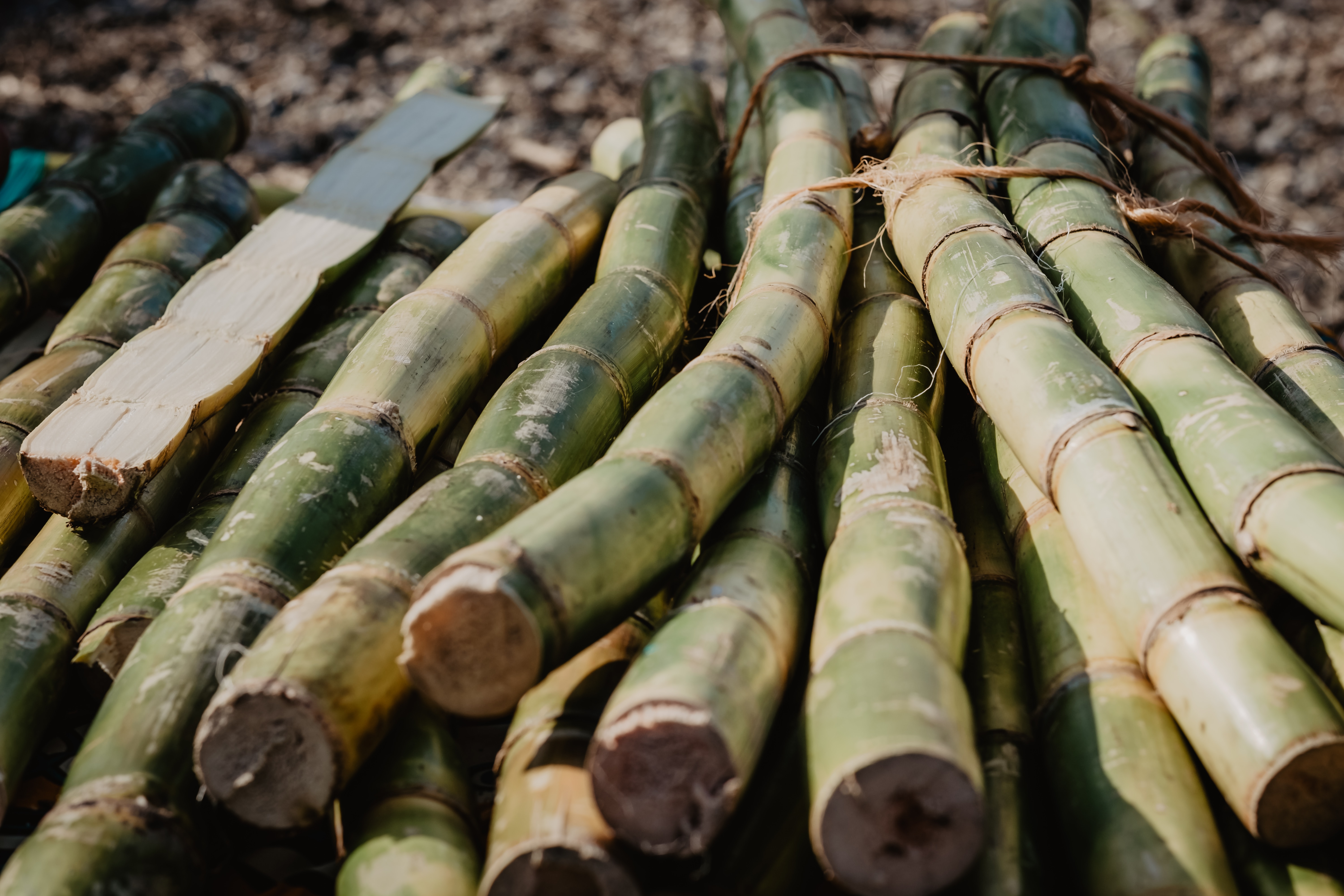.jpg?width=750)
Sam Taylor, the founder at The Good Factory discusses the importance for the textile industry to reduce their GHG emissions and how implementing and scaling bio-based synthetics could provide a solutions.
It’s a well known fact that Scope 3 emissions are where a brand’s carbon footprint is the largest. And the most challenging to manage and reduce. While much has been made of the water consumption of cotton over the years, it doesn’t address the fact that more than 60% of textiles produced are synthetic. Traditionally these have been derived from crude oil, or rather the waste products from the extraction of petroleum. And while they may be called “waste”, which makes up 10% of the crude oil extracted, it provides the oil companies with 40% of their profit. And if there is one thing we know about oil; it produces a lot of greenhouse gas emissions.
For a while it looked like our problems could have been solved with the introduction of recycled synthetics from fishing nets and plastic Coke bottles. Since 1950 we’ve created 6.3 billion tonnes of virgin plastic waste, of which 91% has never been recycled. Many recyclers rely on government support, and on either unpaid or low paid collection. Providing opaque traceability at the feedstock stage, which doesn’t help manage Scope 3 emissions or supply chain confidence. There is many a tale of PET bottles going directly from bottle producer to recycler due to the cost of stopping bottle production or quality failures.
Enter in the new generation of synthetics; Bio-based. These are products with similar characteristics to oil derived synthetics but with a feedstock that is partially, or wholly derived, from renewable resources such as corn starch, sugar cane and plant oils to name but some. Technically these are still plastics and have limited scope for biodegradability and recycling at present. Although Kindra Fibers have launched a scale up project for their bio-based and biodegradable polyester this year. And our own BioAce project; looking at the mechanical recycling of polyamide made from castor bean oil, will be completed shortly. The next 5 years holds a lot of promise.
Unfortunately there is no all encompassing answer as to whether bio-based synthetics are a solution to the climate crisis. It really depends on each raw material and the process that it needs to undergo before it can be turned into a resin. PA10,10, which is made from castor bean oil, doesn’t compete with land for food sources as it grows in very acrid conditions in China and India, and doesn’t require irrigation or fertilisers to grow. As climate change hits these regions quicker it does have the potential to be an income supporting crop for cotton farmers who are already seeing yields reduce. However, it travels more than 11,000 miles to be made into a yarn. Although not too dissimilar in distance to some recycled polyamide yarns.
Farming methods play a big part in how environmentally sustainable any renewable resource is. If deforestation happens alongside tilling the soil for a mono culture crop such as sugar cane, then the damage to biodiversity and soil health will outweigh the benefit of using a carbon sequestering feedstock instead of a recycled plastic. Even when you take into consideration that, according to resin LCAs, there is a 77% reduction in GHG emissions compared to virgin polyester. Although, when comparing LCAs, we do need to be ensure that we are comparing the true lifecycle and production of the product. If a feedstock has been refined in a coal powered facility as opposed to a facility powered by natural gas, then the carbon footprint will be higher. Which is sometimes not accounted for.
As energy costs rise, and further squeeze profit margins, everyone is on the look out for fibres that can be processed and printed with lower temperatures and less resources. One of the benefits of PA10,10 is that it is faster to dye and print, using less water and at lower temperatures than PA6,6 (conventional polyamide), lowering its carbon footprint further. However, it is more difficult to match colour standards than it is for conventional polyamides. The resin supplier of PA10,10 has an LCA with a 55% reduction in GHG emission compared to PA6, with Brugnoli, the fabric supplier who holds the patent for PA10,10 stretch fabrics, has an LCA on their fabrics giving a 25% reduction in emissions compared to PA6,6.
There is no doubt that this a product category that will continue to grow. With forecasts predicting a 25% growth in bio plastics over the next 4 years. In addition to the scaling of Kindra’s bio-based and biodegradable polyester, Invista is adding a partially bio-based lycra to its main collection towards the beginning of 2024. Dyeema launched their partially bio-based yarn in 2020, where 1 metric tonne generates 5 metric tonnes less CO2eq than the same volume of fossil based Dyneema. While Dyneema currently works on a mass balance approach, so bio-based percentages at this time are unknown, they are aiming for Dyneema to be 60% bio-based by 2030. Last year the yarn supplier Radici launched their Biofeel PLA which has similar characteristics to polyester but is 100% biodegradable and industrially compostable, synthesised from sugar cane. Although this yarn is providing some challenges in the production of textiles for apparel, the scope for homewares holds great potential in the near future given the low flammability and excellent UV ratings.
As we inch closer to the global net zero targets of 2030, it will become increasingly important for the textile industry to reduce their GHG emissions. While bio-based synthetics hold challenges to print continuity when switching between conventional and bio-based, there is no doubt that part of the solution will be the implementation and scaling of bio-based synthetics.
For more information on The Good Factory please visit here.
Blog cover image: this image is from Unsplash/Victoria Pressnitz
Topics
Recent news
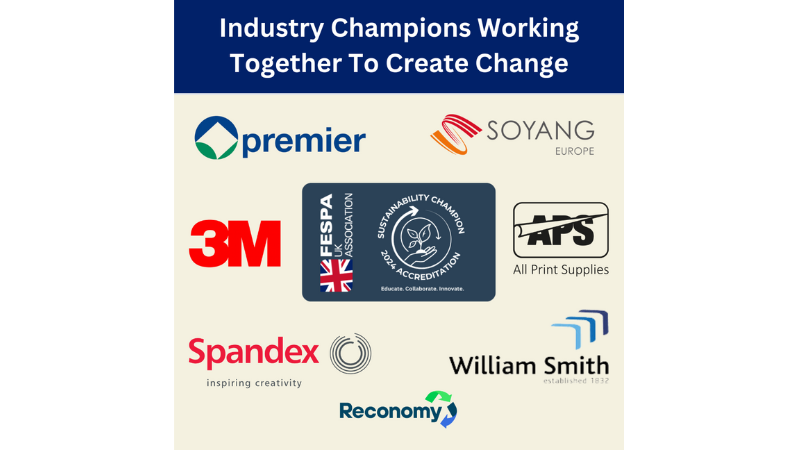_5.png?width=550)
FESPA UK partners with industry suppliers to improve print media recycling
FESPA UK add Self-adhesive Plastics and Siliconised backing papers to their Waste Management Accreditation Scheme and welcomes support from key industry suppliers.
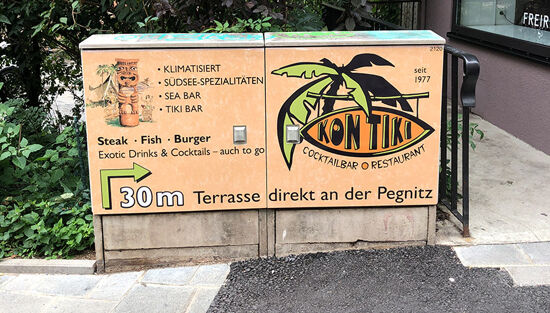
How to print on sustainable self-adhesive films
The printing industry is making substantial efforts to become more sustainable. Sustainable self-adhesive film is an important factor. Sonja Angerer shares how to print on films in an environmentally friendly way and what printers can do to become greener.
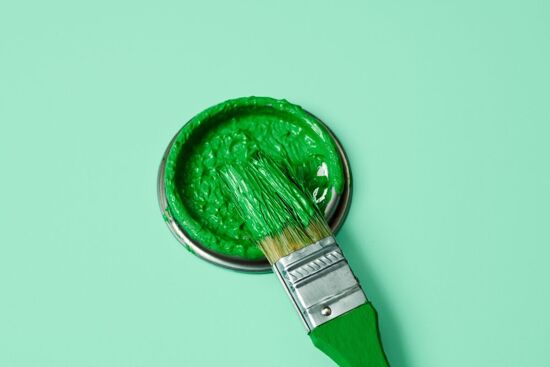
The opportunities and challenges for brands with the EU Green Claims Directive
Steve Lister details the EU Greens Claims Directive which encourages businesses to be responsible and deters greenwashing. It demands accountability from businesses regarding their sustainability. Steve shares the potential penalties for non-compliance, how it will reduce greenwashing, the impact on brands if they are not compliant and the opportunities for brands.
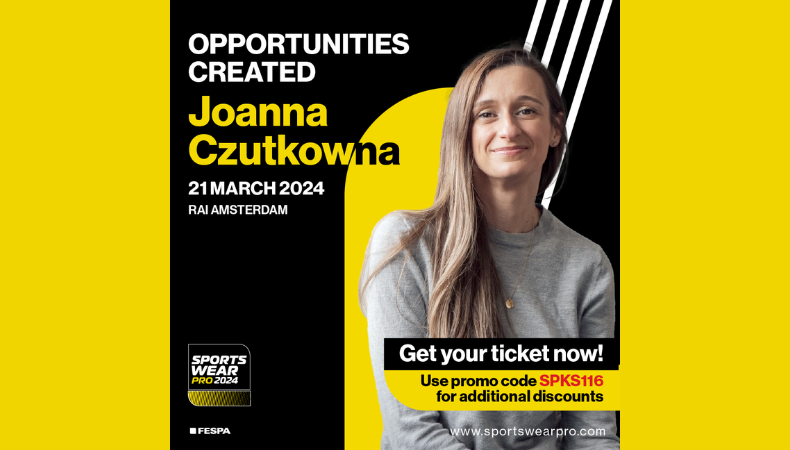.png?width=550)
Sustainable sportswear: Closing the loop for a circular economy
Joanna Czutkowna is a consultant and doctoral researcher specialising in circularity within sports apparel. With over 20 years’ experience managing global sourcing strategy and innovation departments for some of the world's largest brands, she has extensive experience in product development and global supply chains. In this blog, and ahead of the ‘Designing for the Circular Economy’ panel at the 2024 Sportswear Pro conference (21 March at RAI Amsterdam, The Netherlands), she delves deeper into closing the loop with circular garment business models for sustainability benefits.