Building the future: an insight into industrial printing in 2024
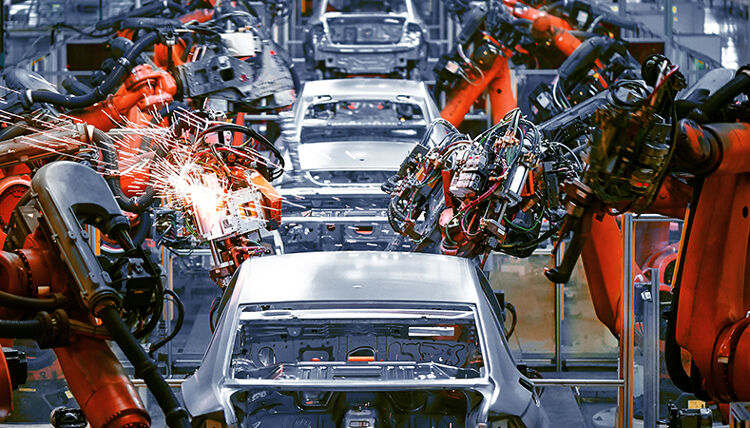
Peter Buttiens, CEO of ESMA, reviews the past year in industrial printing and makes his predictions for 2024.
How was industrial printing in 2023?
During 2023, we noticed that industries linked to energy-intensive production were still suffering from the energy crisis that started in 2022. The glass industry and the chemical industry, including ink suppliers, had difficulties selling volumes in the industrial market.
On the other hand, there were fast-growing segments such as printed electronics in the wearables and healthcare devices. The photovoltaics (PV) market has had an enormous boost in the last few years and continues to look hopeful in the future as new technologies such as perovskite and tandem PV solutions are being released [a perovskite-on-silicon tandem cell has a theoretical efficiency limit of 43% vs 29% for silicon cells].
What challenges does the industrial sector face in 2024?
Industrial printers are looking at entering the market of medical monitoring devices or diagnostic kits for disease testing. These are fail-safe devices, and production quality requirements are at Six Sigma level: the same as in the market for electronic automotive parts.
The demand for perfect products that fulfil specific requirements and meet industry regulations is one of our biggest challenges, and completely different from the normal printing market of posters, textile and packaging where image quality and colours play the most important role. Here we enter an unknown area where an electronic or chemical potential failure is critical in both short- and long-term use.
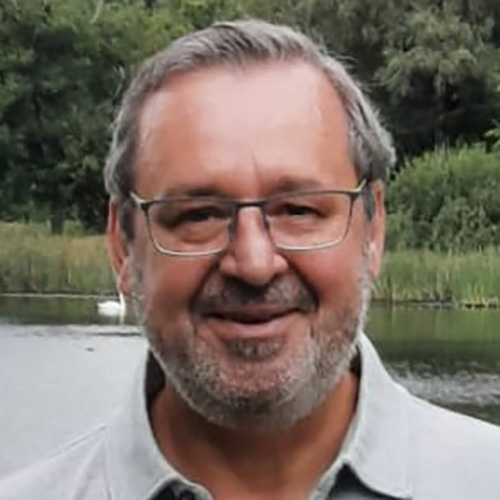
What have been the most notable recent innovations?
There has been a great demand for fine line printing, for PV and printed electronics in general, which is pushing screen printing to go towards 10 micrometres.
We are seeing many new print technologies emerge: high-precision capillary printing for micron and sub-micron. Other technologies, such as continuous laser-assisted deposition (CLAD) and laser-induced forward transfer (LIFT), are important for the deposition of new materials that are less typical than printing inks but more material-based (copper, silver and other solid based materials). This is important for the next generation of wearables for medical or daily use in our lives.
What does the regulatory landscape look like?
Many new directives have been introduced for recycling and waste reduction for products reaching their end of life. The first is the EU’s Eco-Design for Sustainable Products Regulation (ESPR). The main goal is that by 2030, the new sustainable products framework can lead to 132 million tonnes of oil equivalent of primary energy savings, which corresponds to roughly 150 billion cubic metres of natural gas. The proposal establishes a framework to set eco-design requirements for specific product groups (also printed products) to significantly improve their circularity, energy performance and other environmental sustainability aspects. It will enable the setting of performance and information requirements for almost all categories of physical goods placed on the EU market.
The second is extended producer responsibility (EPR). Here, the focus lies on shifting the responsibility for the treatment and disposal of certain waste streams to producers. It also aims at promoting the recovery and recycling of waste, reducing landfill and encouraging the development of circular economy business models. It has been implemented for a range of waste streams, including packaging, batteries and electrical and electronic equipment, but will be widely extended to textile and packaging and other printed materials.
Through its conferences and training courses, ESMA educates on industrial print technologies
How are customer demands changing?
Industrial printing is a highly price-sensitive market unless the product is extremely special and outstanding. Demands from customers in the industrial sector are different because they discuss sub-parts, and more functionality is integrated in a single piece. An example is in-mould decoration, which is now moving towards in-mould electronics (IME) and then to 3D-IME – with onboard electronic chips integrated into the final part. This has been achieved in automotive, an extremely high-demanding market, within less than a decade. Today, the possibilities seem to be endless and are sure to measure up to the shift towards electric vehicles.
Is it a challenge to attract skilled workers?
The biggest challenge is to find the new skill profiles for industrial printing. Applicants need to have an engineering background (materials, chemistry, electronics, bio and so on) for their specific industrial print segment. In our ESMA Academy training sessions, we have seen that attaining knowledge of materials or chemicals and how to handle them during printing are the biggest challenges for new markets. We notice the trend towards new sustainable and functional technologies. The switch from large volumes towards shorter and more variable runs is another important factor for the future.
What do you think the role of artificial intelligence (AI) is and will be in industrial printing?
AI developments can be mostly observed in design and RIP software, which is a natural link. AI supports customers in designing their individualised products in an optimal way.
But there are other possibilities too: for example, AI can be used in the selection of materials and chemicals for optimising print possibilities and material concepts. AI can help develop new and more complex inks with specific functionalities. This is very important in biomedical printing, which applies lab-on-a-chip for diagnostic kits and other disease testing methods (such as COVID tests).
We know that the pharmaceutical companies are looking to printed medications that are adapted more to the needs of the patient (weight, age and gender), to optimise the needs and step away from standards. Without support from automation, robotisation and AI, these kinds of project would be impossible.
Become a FESPA member to continue reading
To read more and access exclusive content on the Club FESPA portal, please contact your Local Association. If you are not a current member, please enquire here. If there is no FESPA Association in your country, you can join FESPA Direct. Once you become a FESPA member, you can gain access to the Club FESPA Portal.
Topics
Recent news
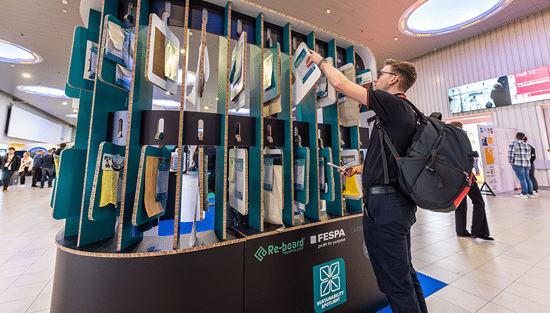
New sustainable materials at Sustainability Spotlight
Sustainability Spotlight returned by popular demand to FESPA Global Print Expo last month in an exhibit curated by The Good Factory.
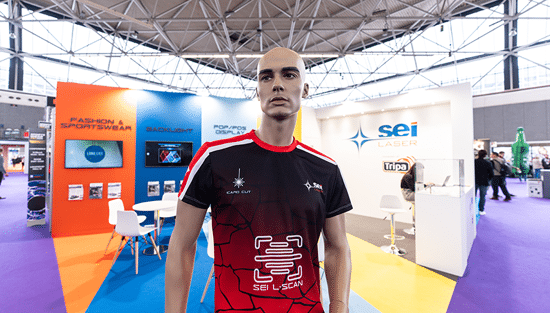
Sportswear Pro: building ‘Brand Me’
After the success of the inaugural Sportswear Pro last month, we spoke with panellist and personalisation expert James Lawrence-Jones about the most exciting revelations at the event.