Process control: sticking to the standards
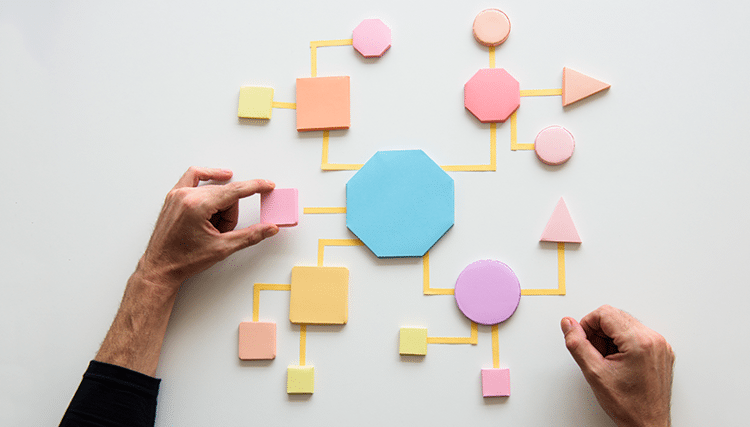
Paul Lindström shows how following ISO standards can help to streamline the print production process.
When you apply process control on a production workflow, it’s clever to use established standards as much as possible. Within graphic arts production, the most commonly known and most widely used standard is definitely the ISO 12647 series (process control for the production of halftone colour separations, proof and prints). Part 2 specifies how optimised offset printing should be done, part 5 specifes how to optimise screen printing in four colour process, and part 7 specifies aim values and tolerances for digital (contract) proofs.
No quality control is possible without process control
Unfortunately, there aren’t any standards for the different types of digital production print, since it has been impossible to agree on standardised aim values for the very many types of inks used in digital printing. With absent international standards, the ISO 12647-2 standard for offset is commonly used as a de facto reference standard for many types of digital printing. In effect, the digital press acts as a proofing device, and by checking that the colour deviation isn’t larger than what is acceptable for the print buyer, you can validate that the production print is compliant to the standard you and your customer have agreed on.

It’s important to view prints and proofs in a viewing booth compliant to the
But there are other useful ISO standards that can help when setting up your workflow with full process control. ISO 3664 specifies the criteria for accurate viewing booths and ISO 13655 specifies the characteristics of a spectrophotometer. And then there is the ISO 15930 series, which specifies how print-ready PDFs should be created according to the PDF/X-standard. A soft proofing system should comply to both ISO 12646 and ISO 14861 – and the list goes on.
Adhering to standards can help in applied process control and also when streamlining the print production process. Process control should increase throughput and capacity, and so ensure productivity and profitability. All fit well into the business model of print on demand and the use of web-to-print solutions to capture more jobs with as little manual intervention in the order and the production processes as possible.
But it all stands or falls with having a robust quality management system in place. And no quality control is possible without process control.
- Paul also writes for Club FESPA about the most current process control thinking, and lists the best ways to measure quality.
Become a FESPA member to continue reading
To read more and access exclusive content on the Club FESPA portal, please contact your Local Association. If you are not a current member, please enquire here. If there is no FESPA Association in your country, you can join FESPA Direct. Once you become a FESPA member, you can gain access to the Club FESPA Portal.
Topics
Recent news
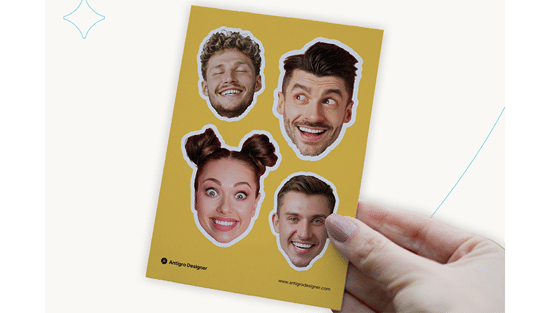
How bespoke sticker production can boost revenue
We spoke to Antigro Designer about its new client-tailored software that aims to reinvent sticker production.
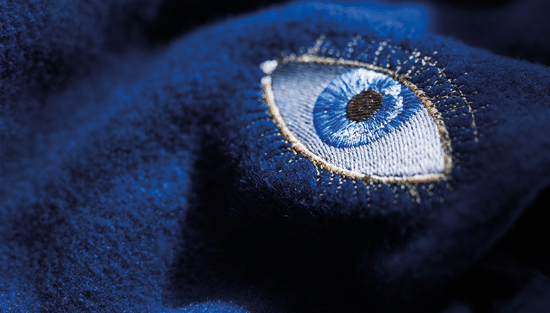
Multicoloured embroidery on demand
Conny Svanberg, digital embroidery expert at Coloreel, and exhibitor at the Personalise Make Wear feature at Personalisation Experience and Sportswear Pro 2024, discusses dye sublimation and colour management.
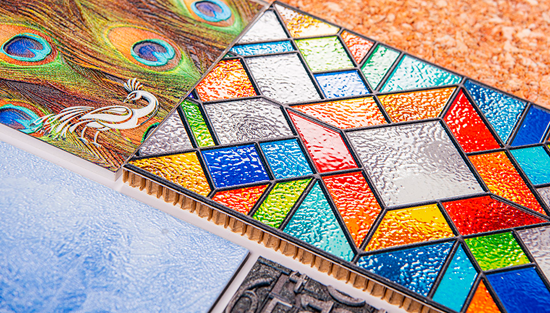
Getting started with haptics: swissQprint
Carmen Eicher, Chief Sales and Marketing Officer, swissQprint and Claudio Müller, Application Engineer, discuss the business of building haptics.
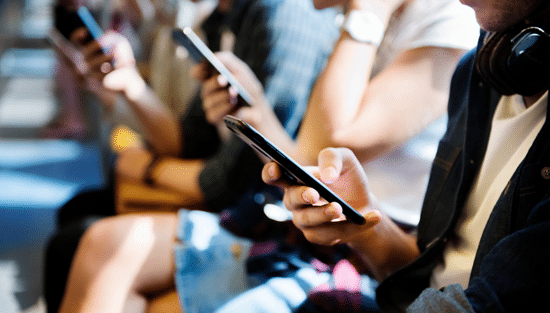
How print businesses can have better relationships with new, young staff
Recruitment and retention remains a problem in many print businesses. We spoke to best-selling author and expert in emerging generations Chloe Combi about how printers can maximise their relationship with young workers.